Guides
Common Machinery Hazards & Controls Technical Guidance
In the world of Plant and Equipment, there are plenty of interesting topics to discuss, especially in relation to the management of safety hazards and risks.
Ideagen Plant Assessor’s guidance in this area is focused on sharing useful information on specific plant and equipment hazards, the various controls available or required, ensuring your controls are adequate along with long term machine safety management.
Ideagen Plant Assessor software considers thousands of hazards associated with different types of plant and equipment, so there is no shortage of topics for us to share with in this section.
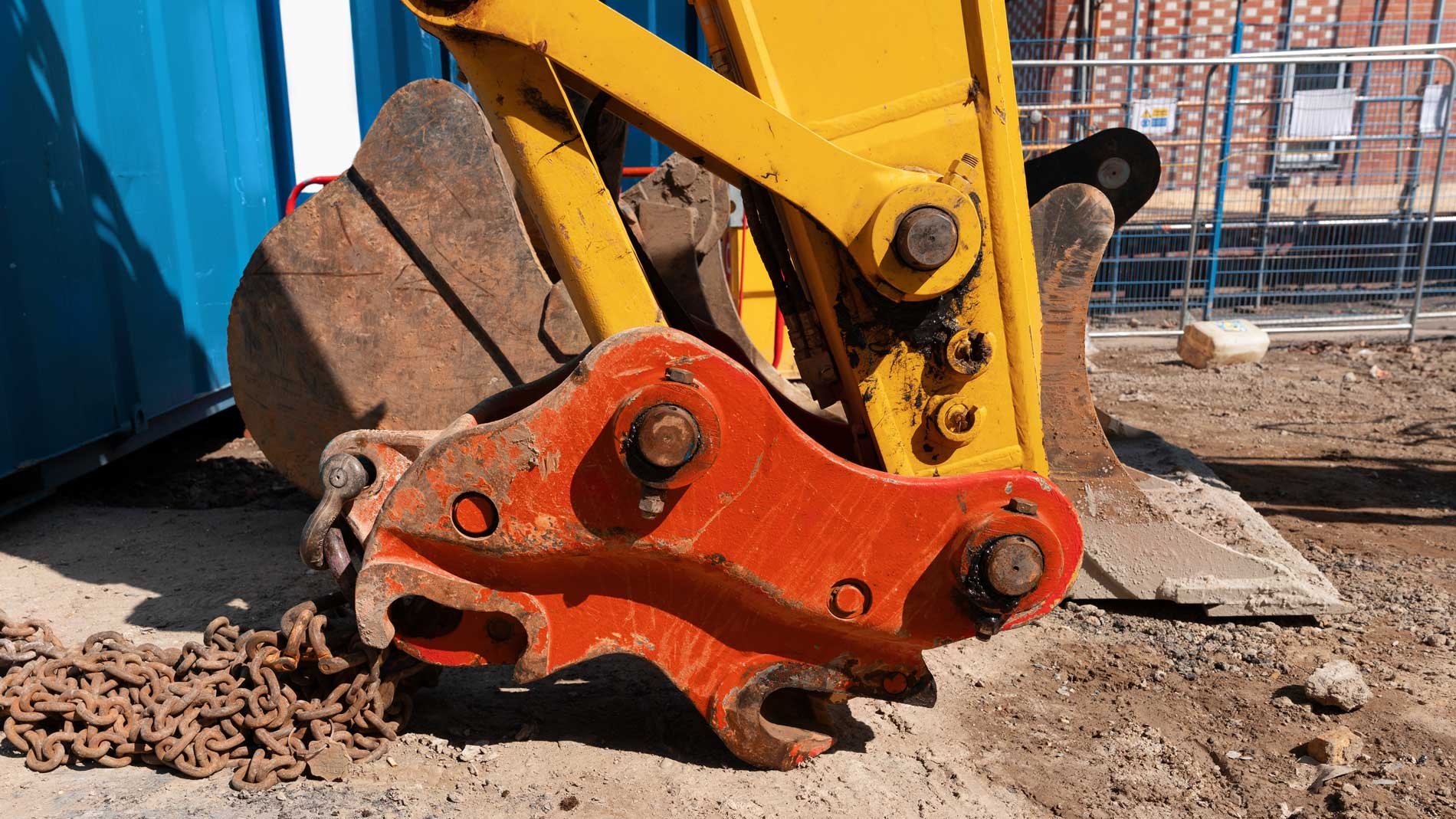
Standard Update: AS13031:2023
Learn about key elements of the new standard AS13031:2023.
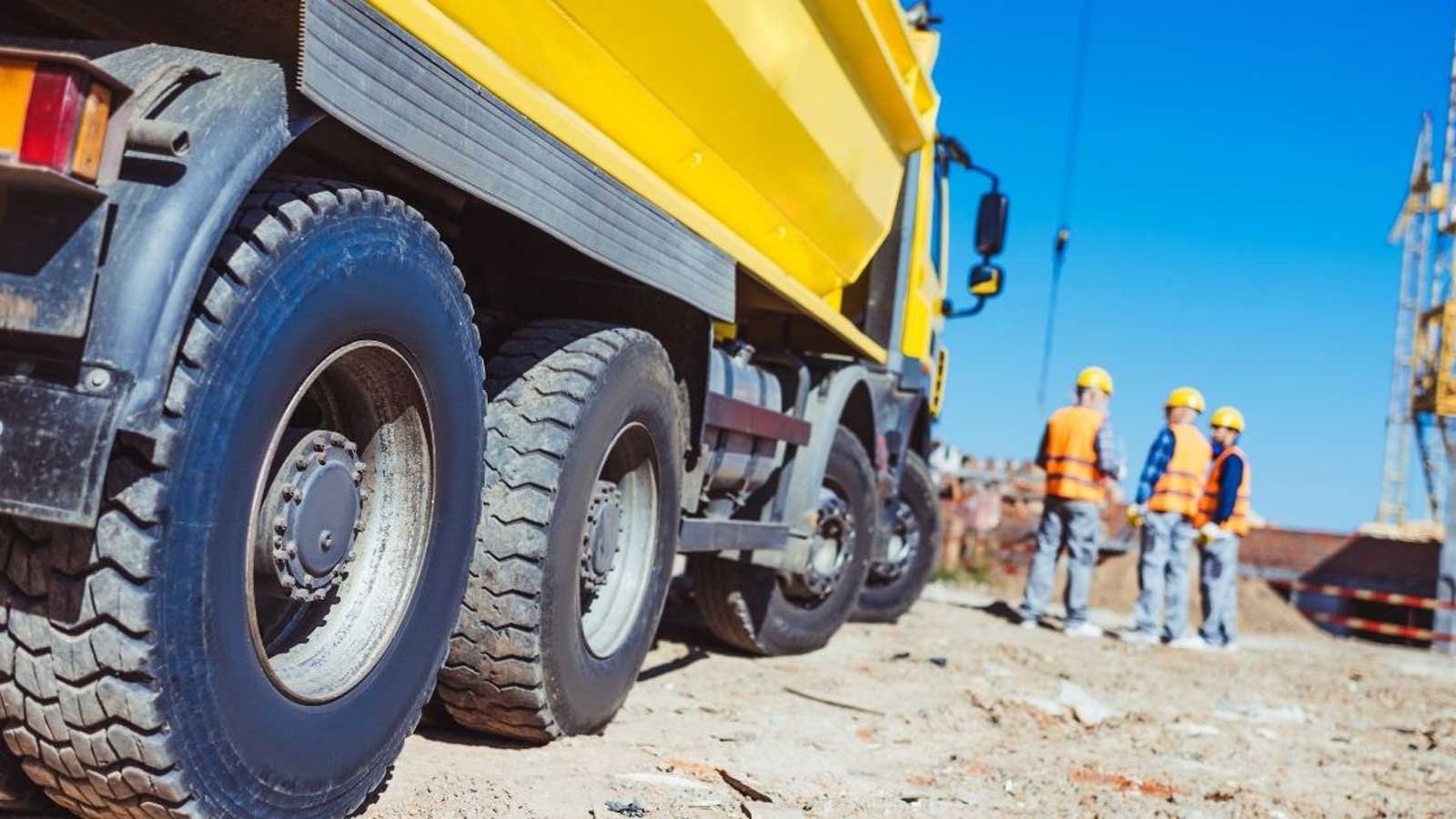
Australian Standards 4024 Series
Check out the 4024 Safety of Machinery standards
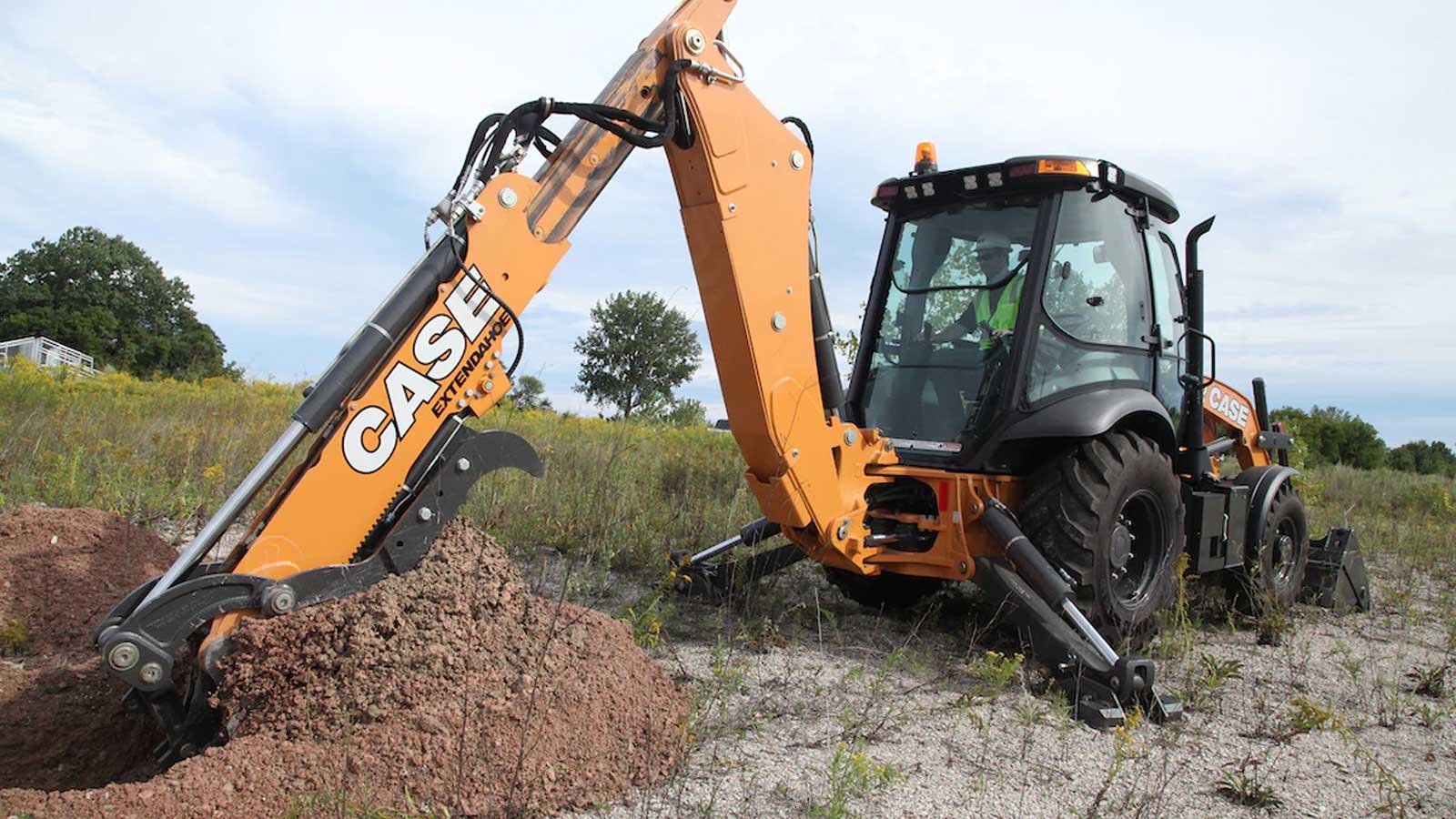
Backhoe Stabiliser Legs
Find out why stabiliser legs are important on your backhoe loader.
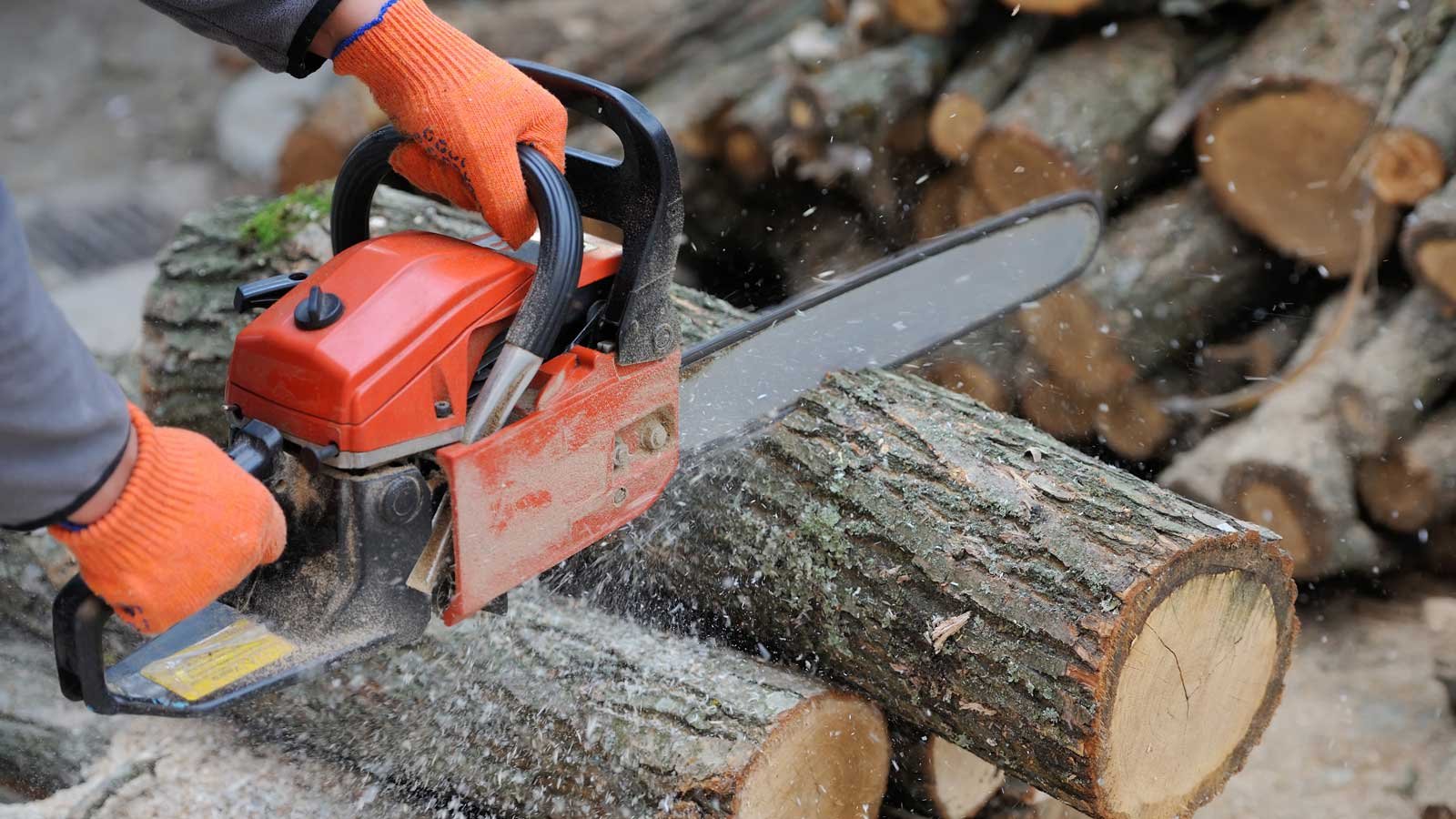
Chainsaws
Hundreds of Australians are injured while operating a chainsaw each year.
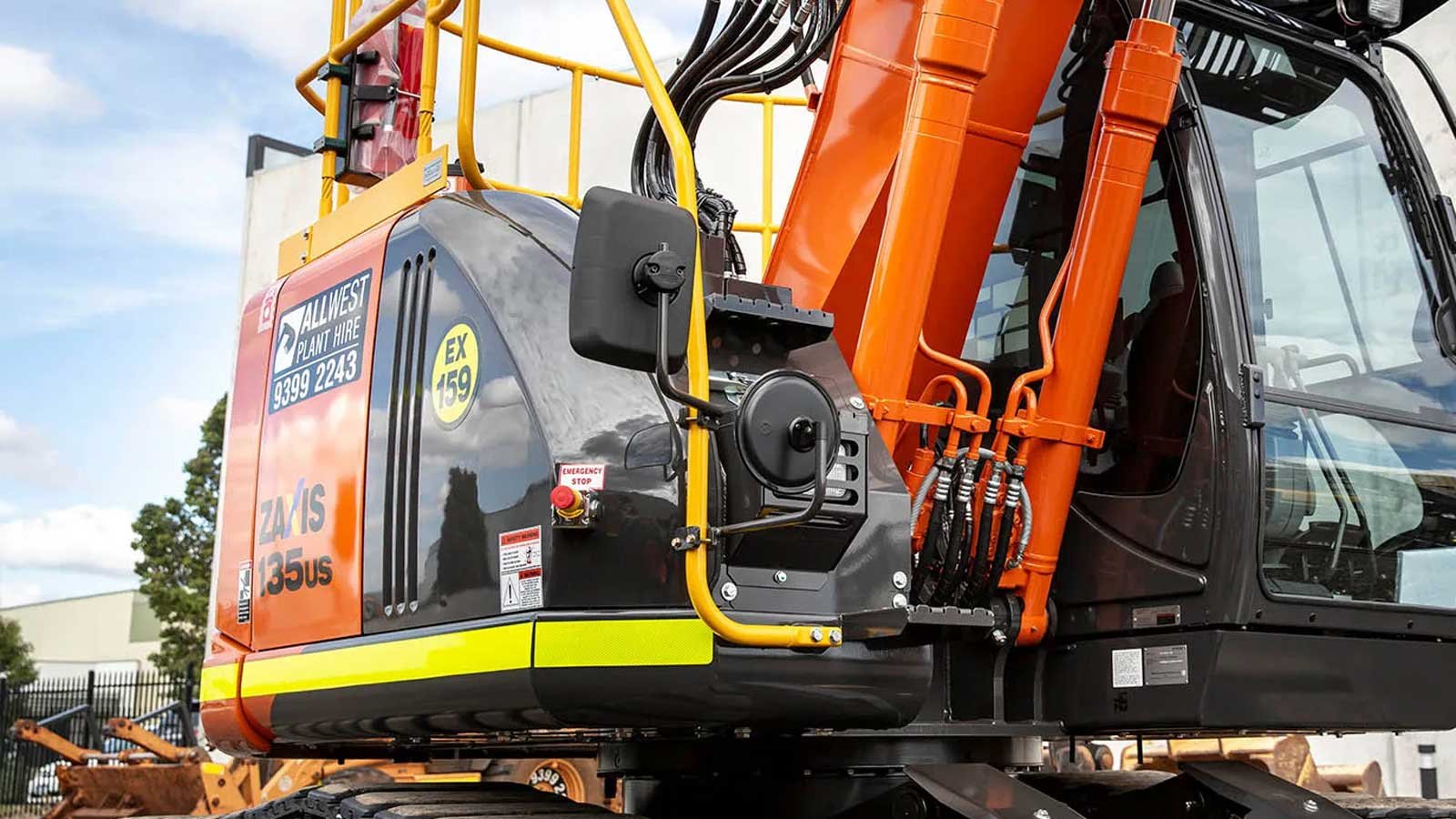
E-Stops
Find out all you need to know about e-stops.
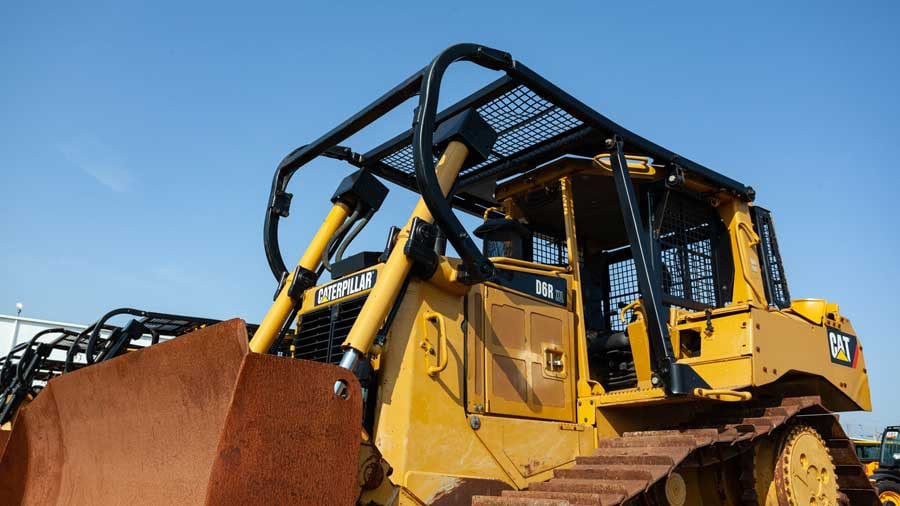
FOPS 1 or 2?
FOPS are Operator Protective Devices designed to protect from items that may fall on a piece of machinery while operating. Learn which one you need.
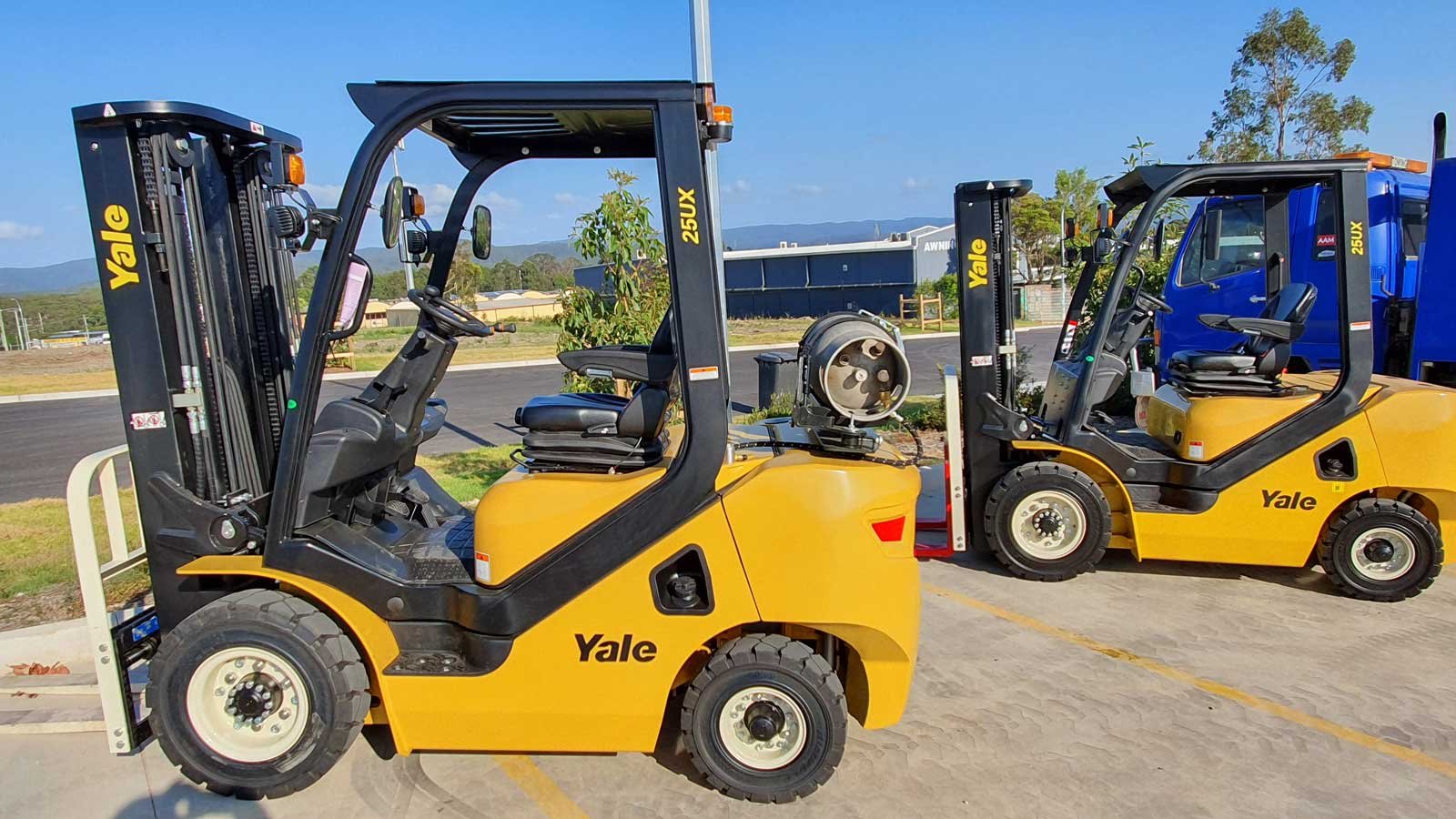
Gas Forklift Standards
We regularly field questions on what to do if a forklift has AS1425 quoted instead of AS4983.
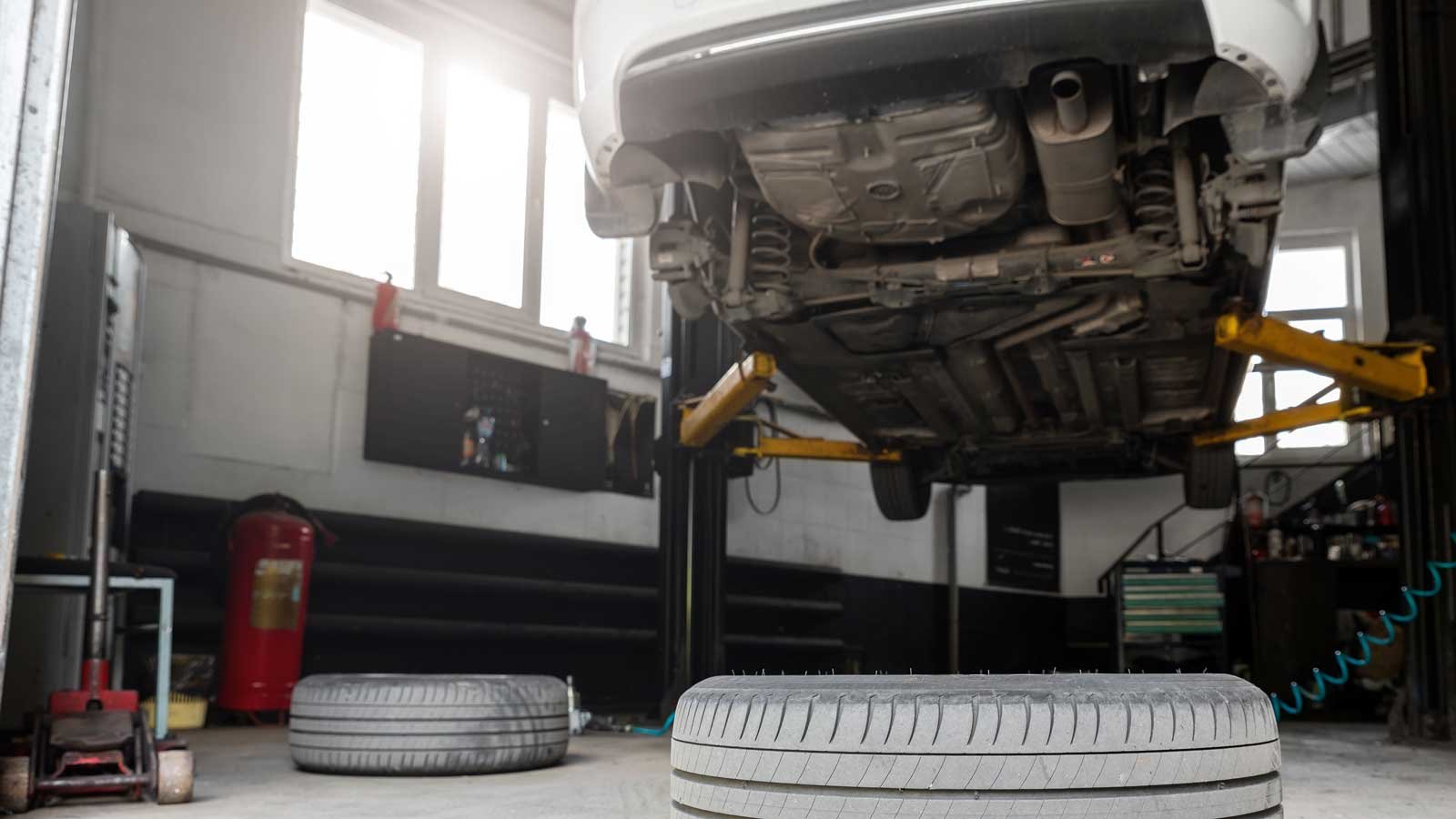
Hoists
Some hoists do not meet Australian standards. Find out what you should look for when purchasing a hoist.
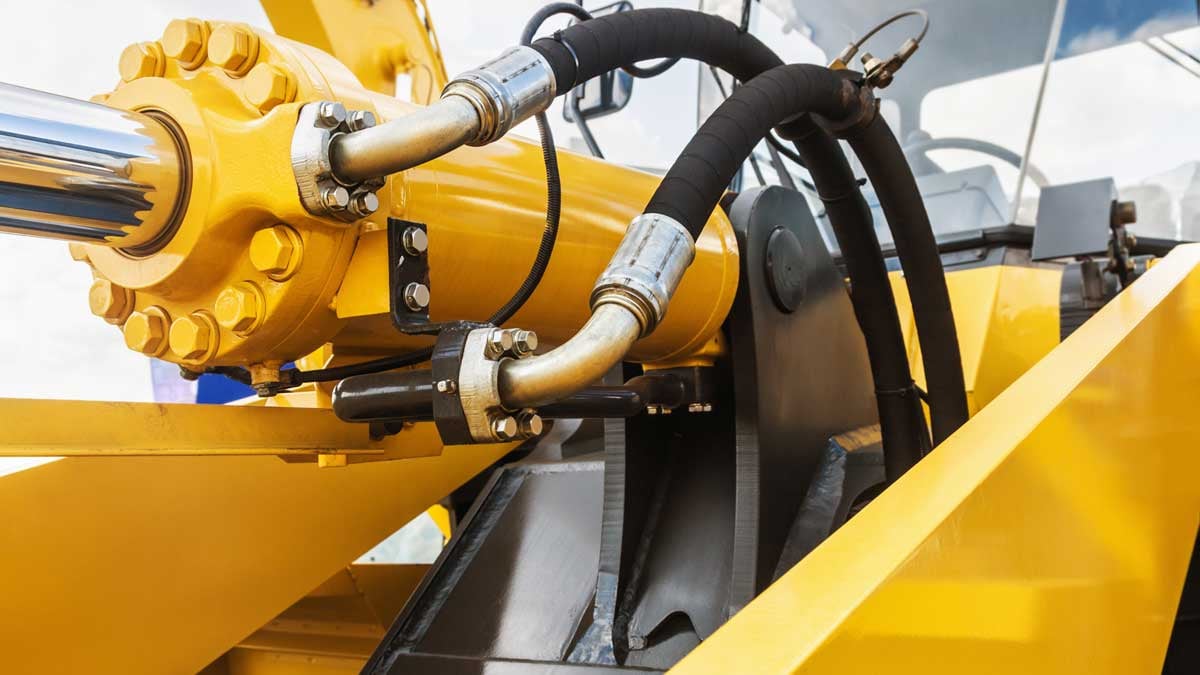
Hydraulic Hose Safety
Hydraulic system components run at significant pressures and temperatures, posing hazards.
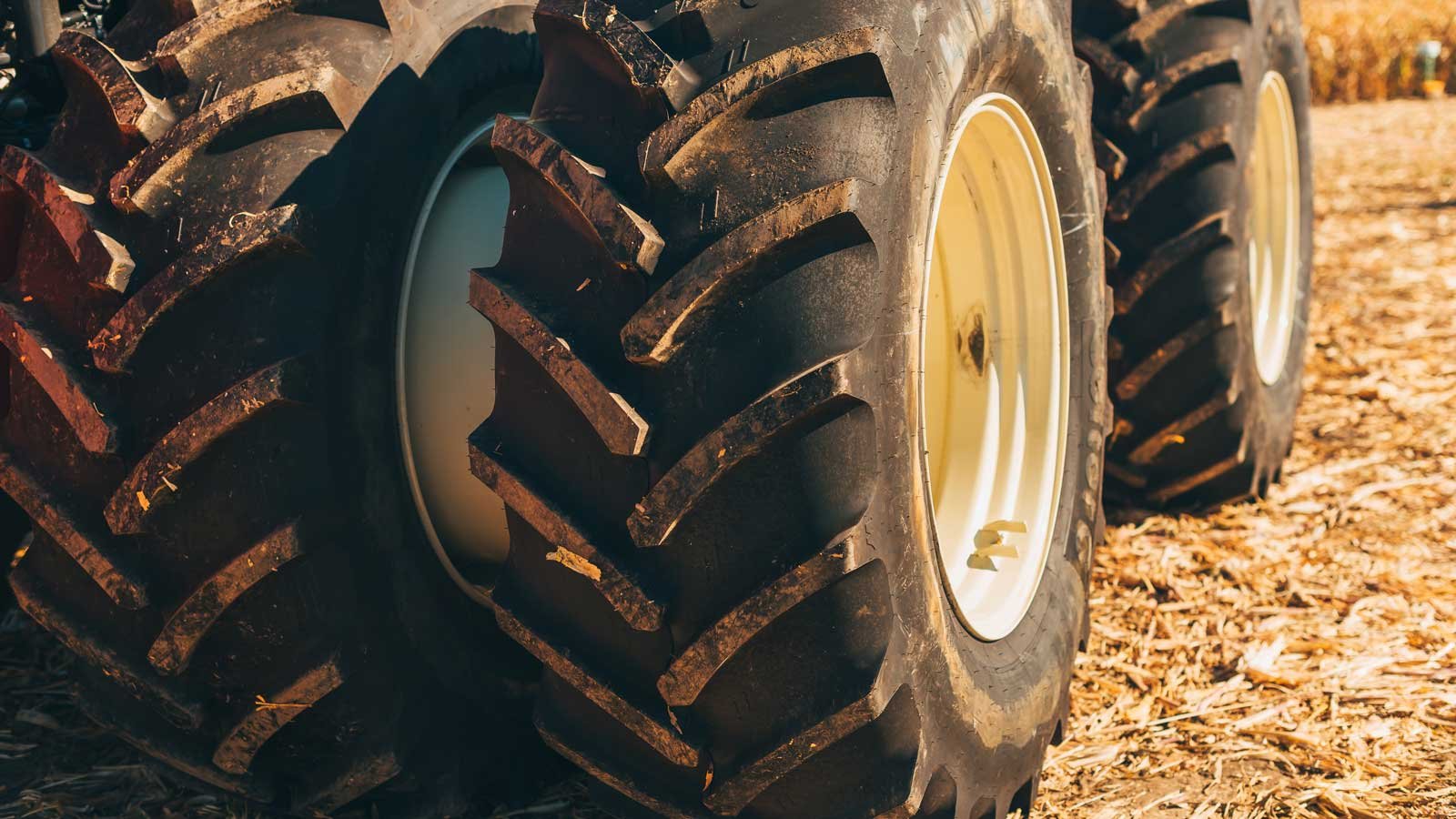
Inspecting Tyre Condition
Tyres are used on a wide variety of vehicles and machinery and their condition is often overlooked.
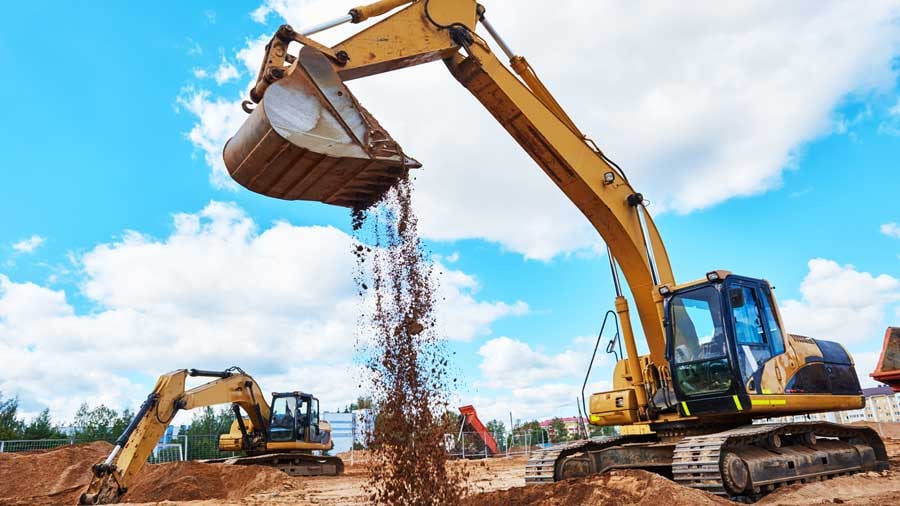
Lifting Capacity
The lifting of any freely suspended load is a high risk activity. Learn the need for lifting capacity labels on earthmoving machines.

National Heavy Vehicle Regulator V3
Find out about the National Heavy Vehicle Register SVB6 Version 3.
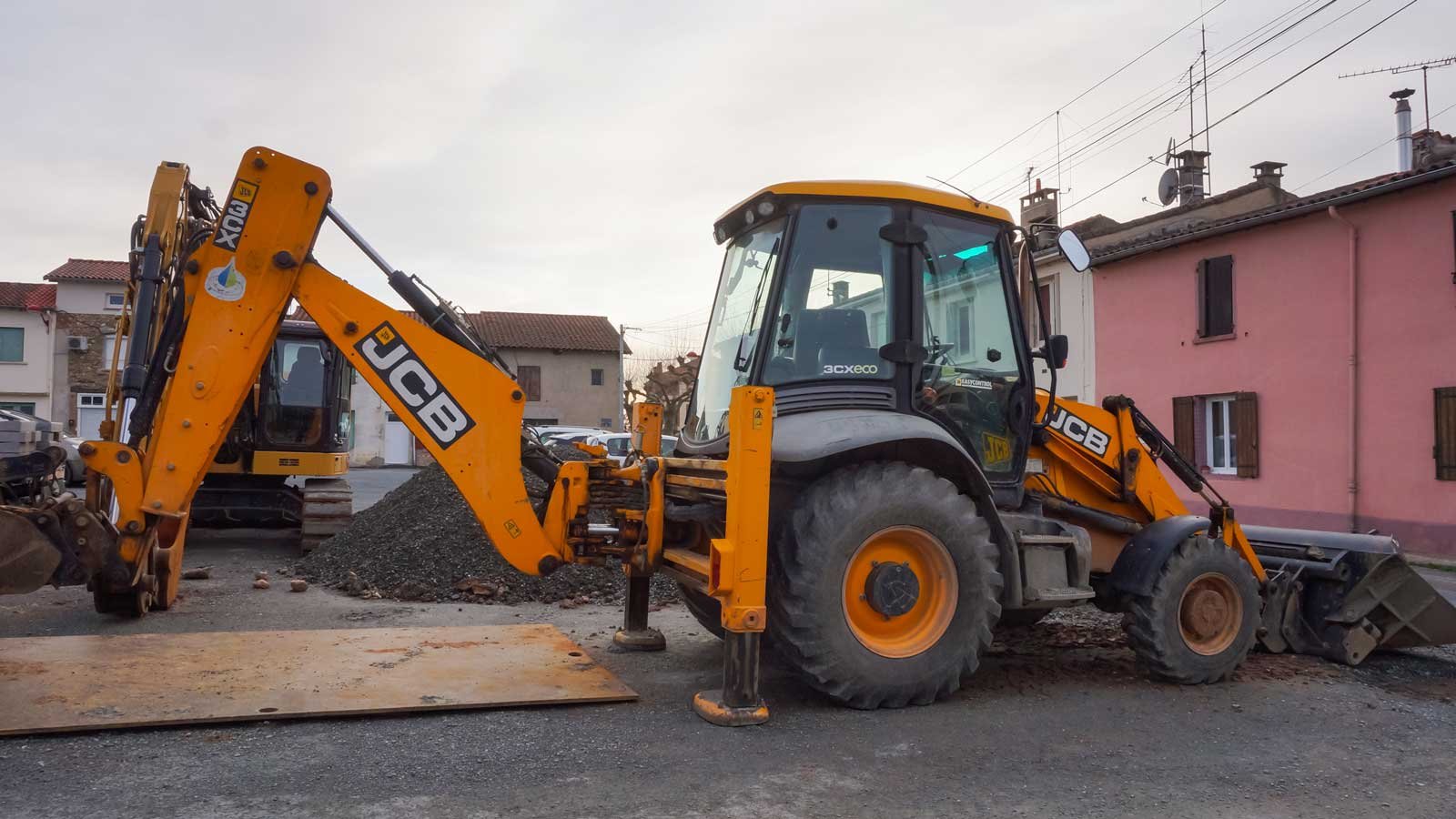
Neutral Start Controls
To reduce the risk of uncontrolled movement at startup, a neutral start control is needed. A Plant Assessor inspection can help.
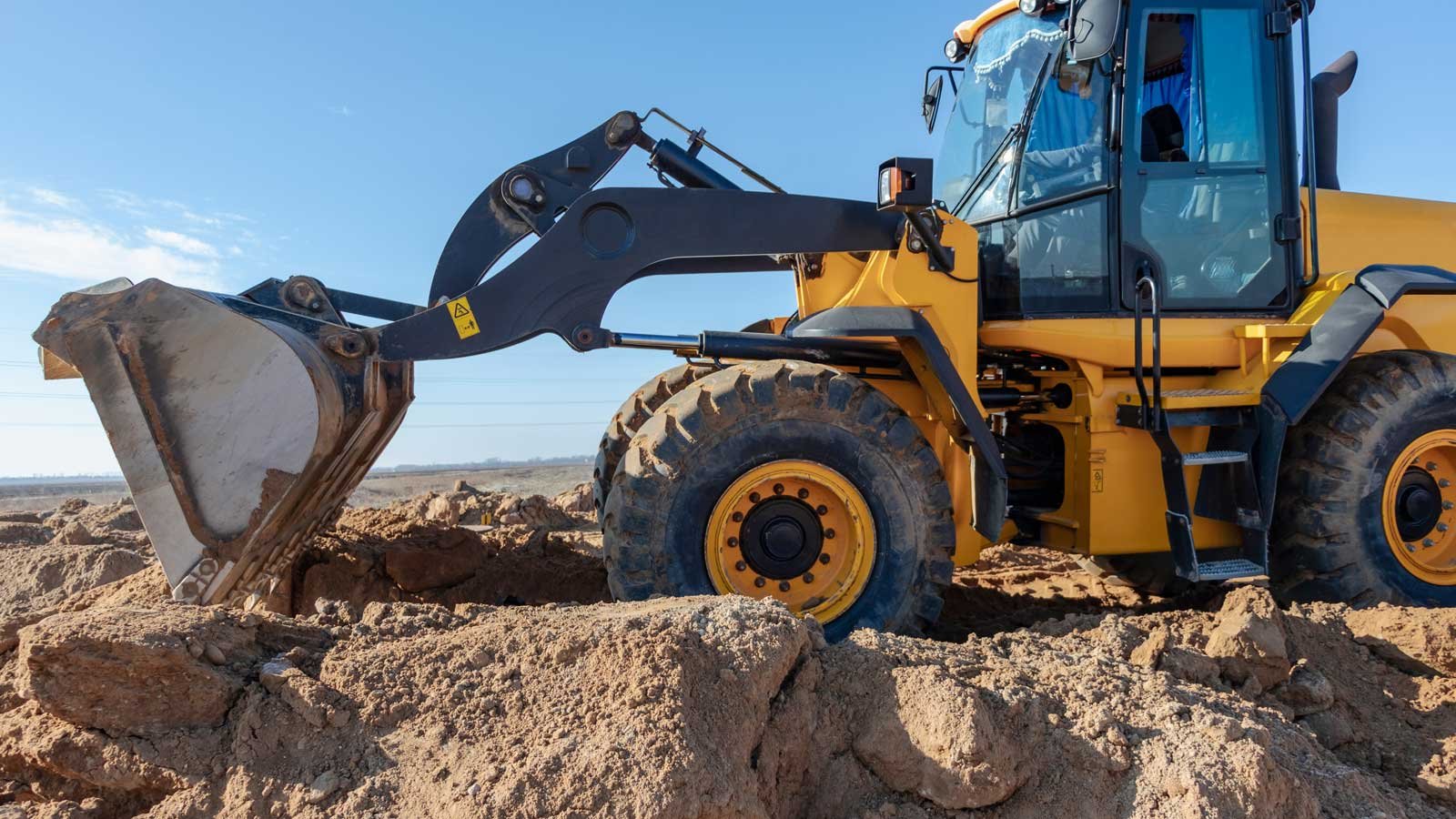
NSW Quick Hitch Position
SafeWork has released a revised position paper, expanding on and clarifying its position on quick hitches.
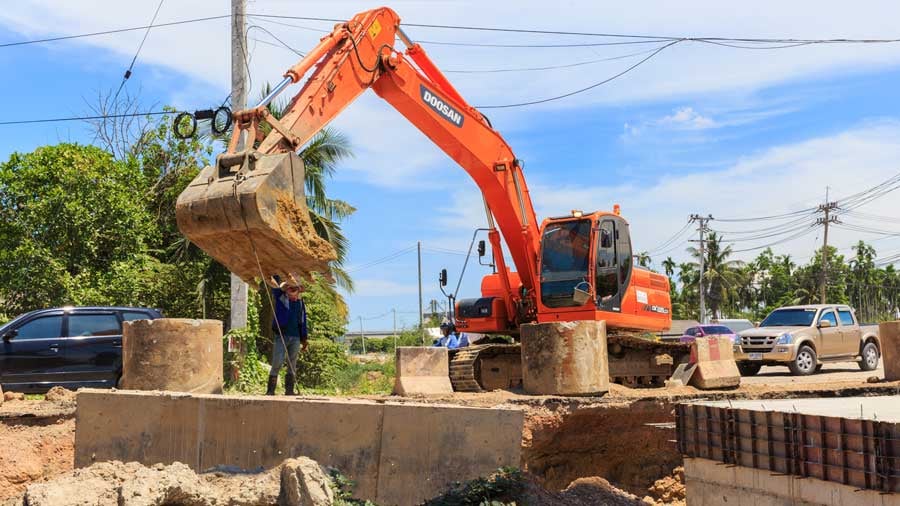
Plant & Powerlines
Ensuring safe systems of work for plant around powerlines can be challenging.
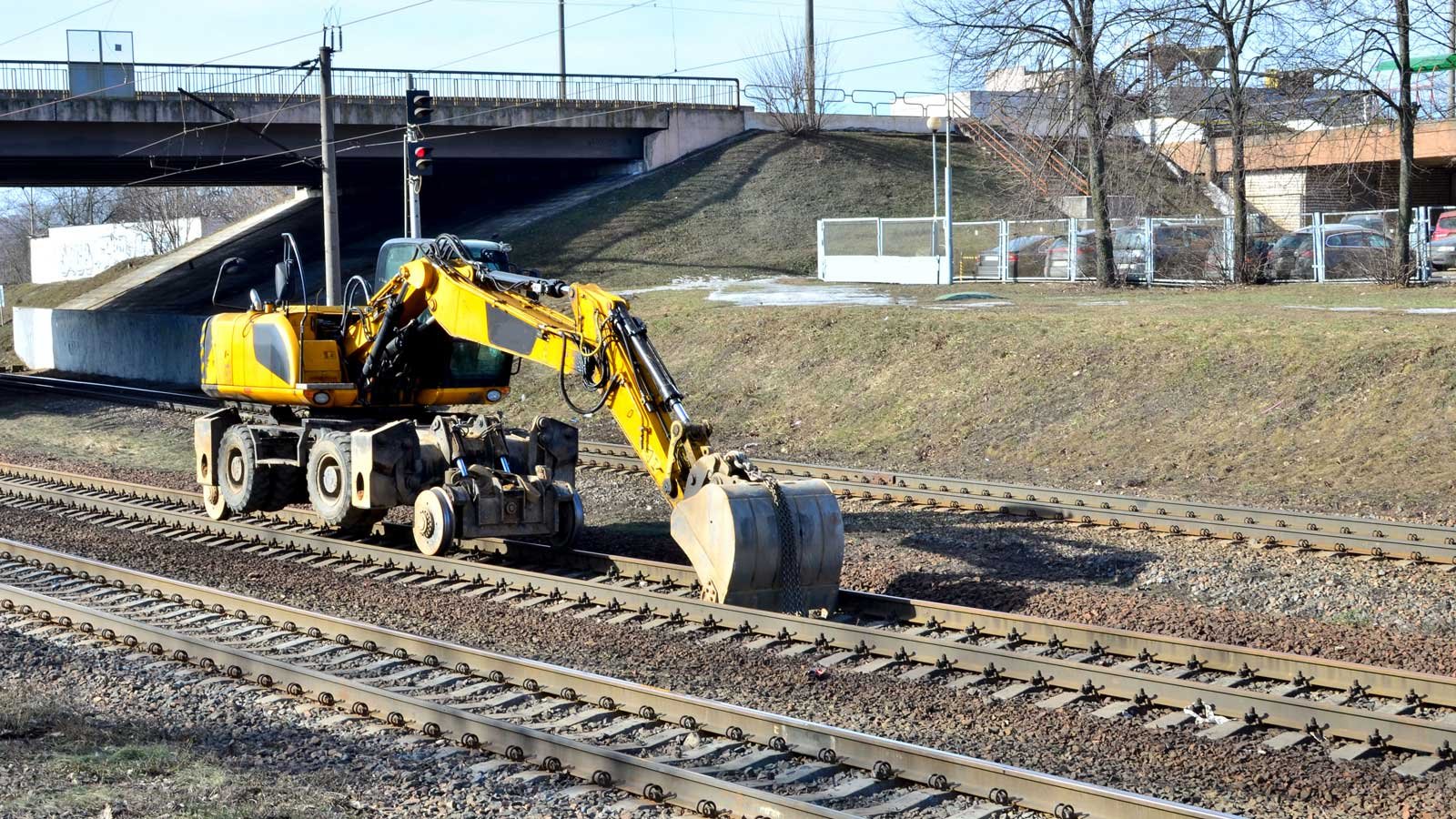
Road Rail Vehicles
The Rail Industry Safety Standards Board (RISSB) has released new standards for the assessment of Road Rail Vehicles.
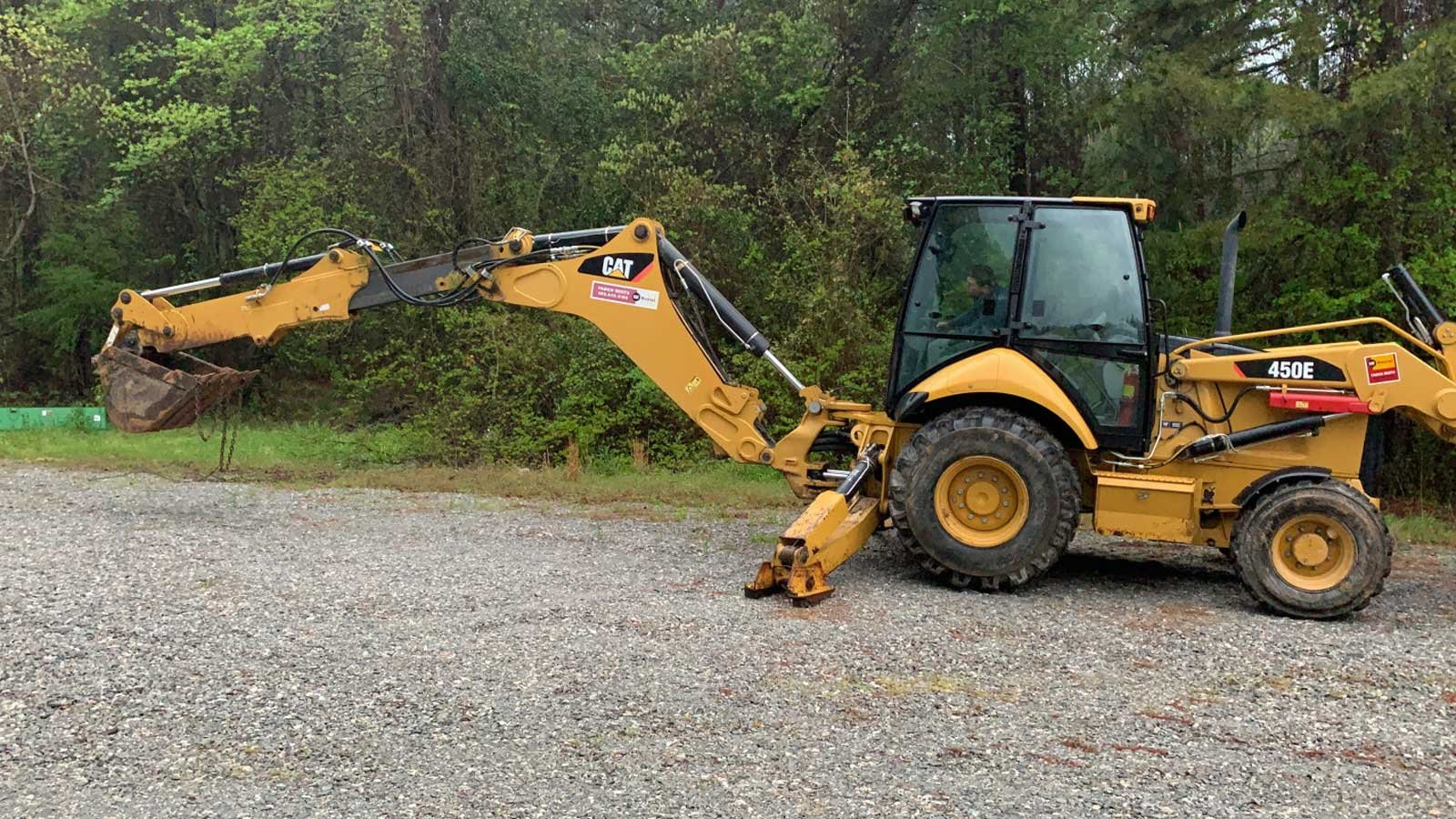
Safety Props on Loaders
Why don’t all loader risk questionnaires in Plant Assessor ask for a mechanical safety prop?
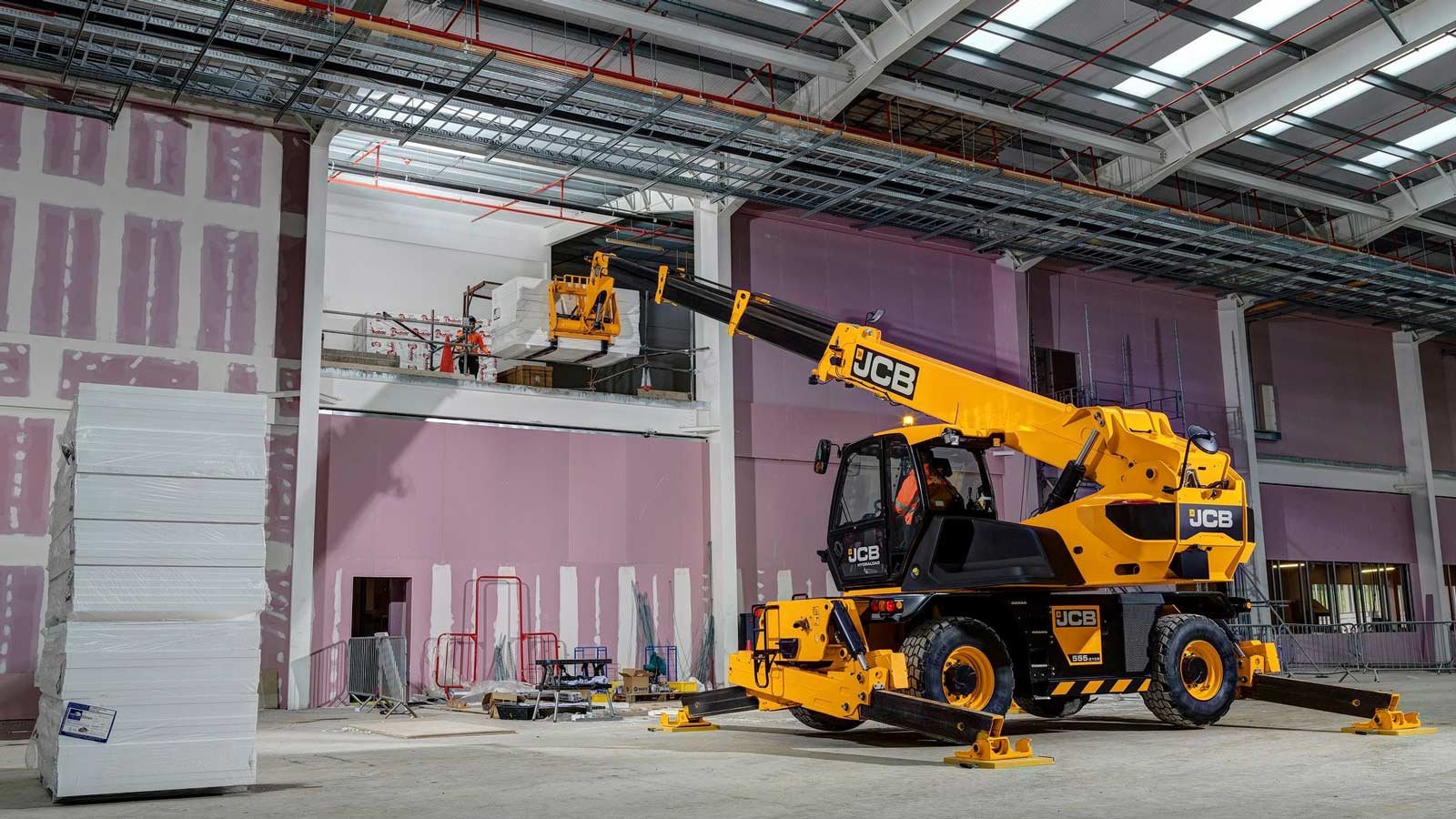
Slewing Tele Handler
Find out all you need to know about the slewing tele handler.

Split Rims
There are many hazards associated split rims. Find out what to be aware of.
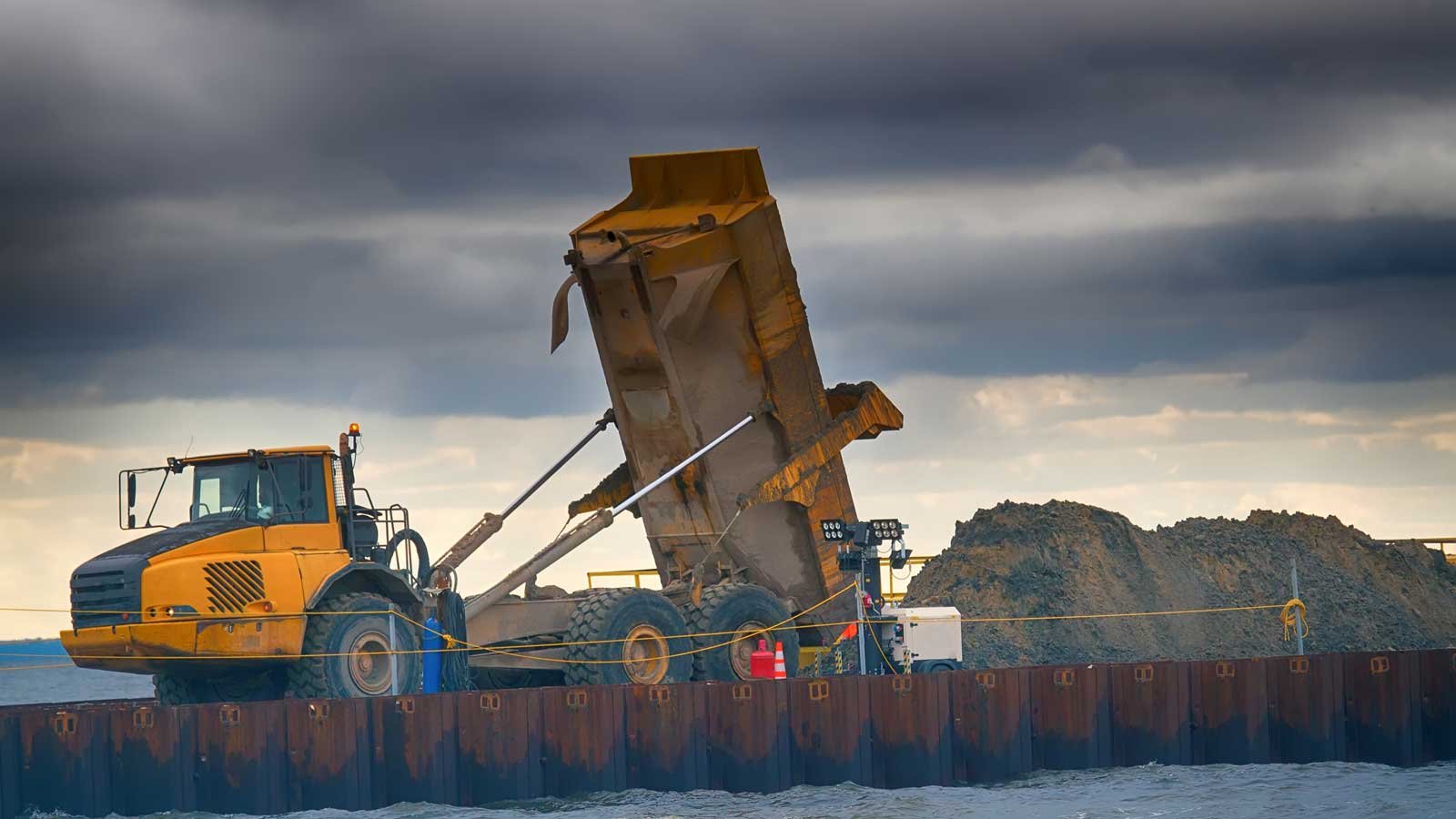
Tip Truck Hoisting Systems
We regularly receive questions regarding tip truck hoisting systems. Find answers here.
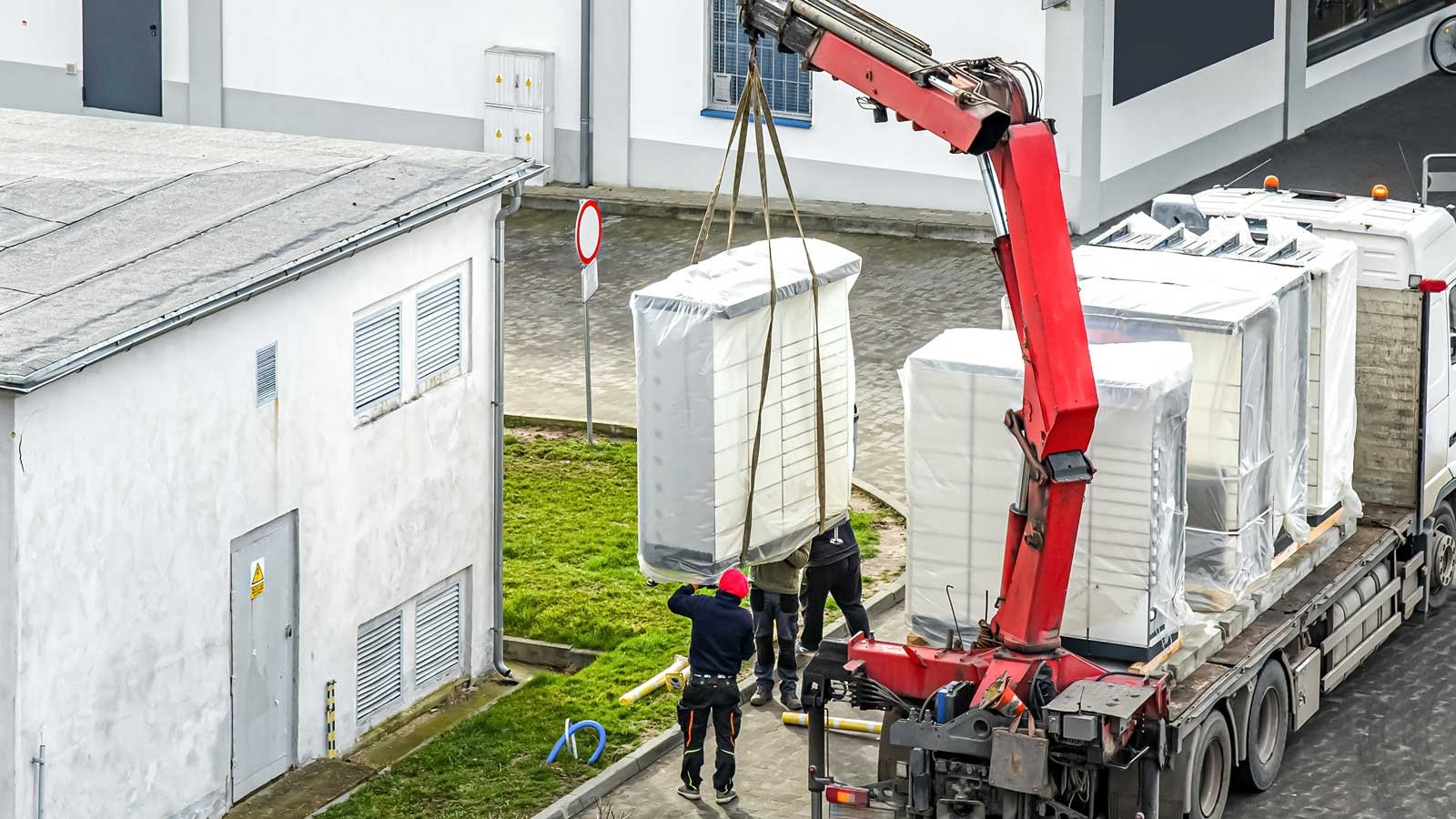
Vehicle Loading Cranes
An updated edition of AS2550.11 has been released.
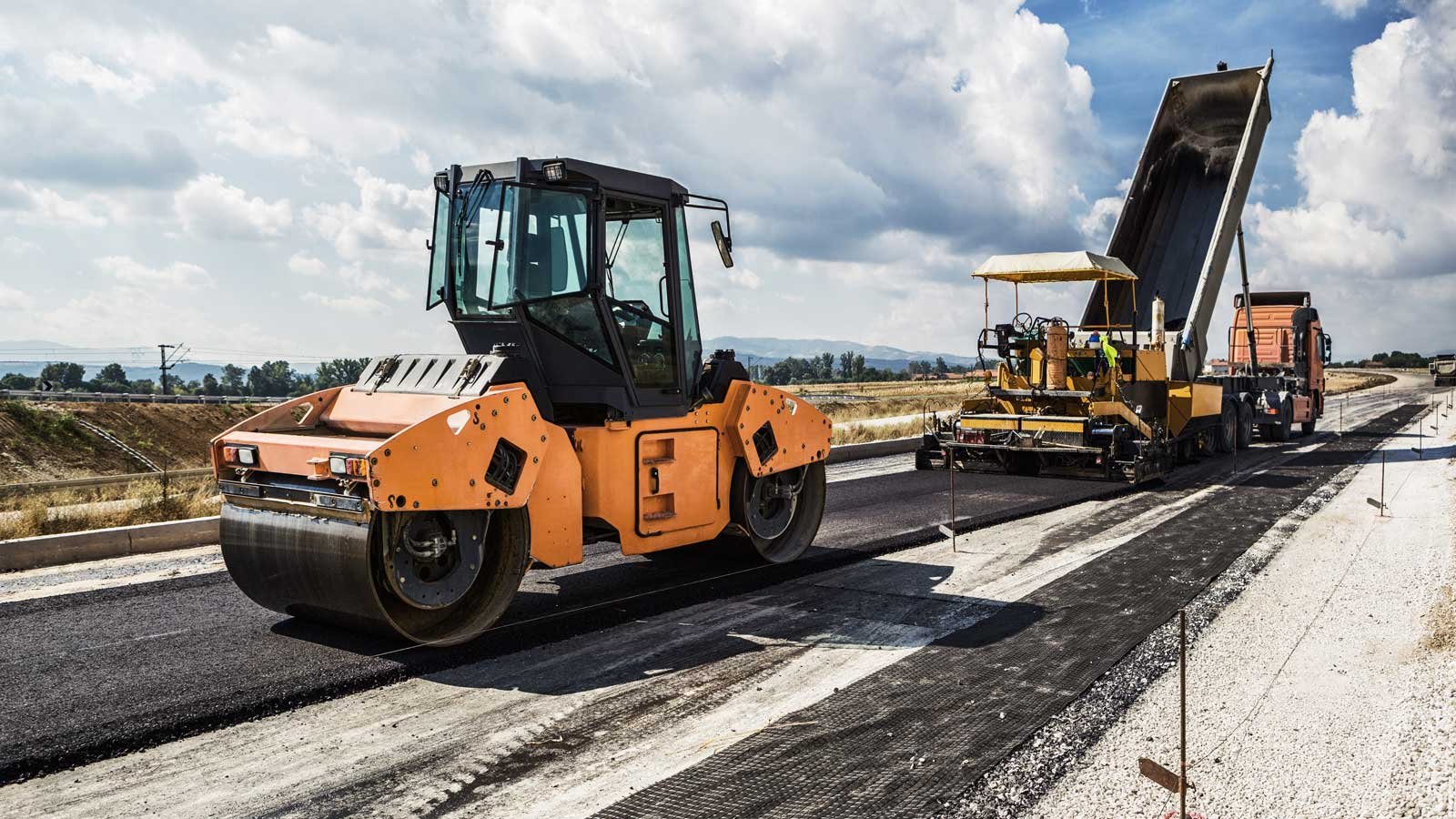
Conducting our Risk Assessments
Everything about conducting a risk assessment in Plant Assessor.
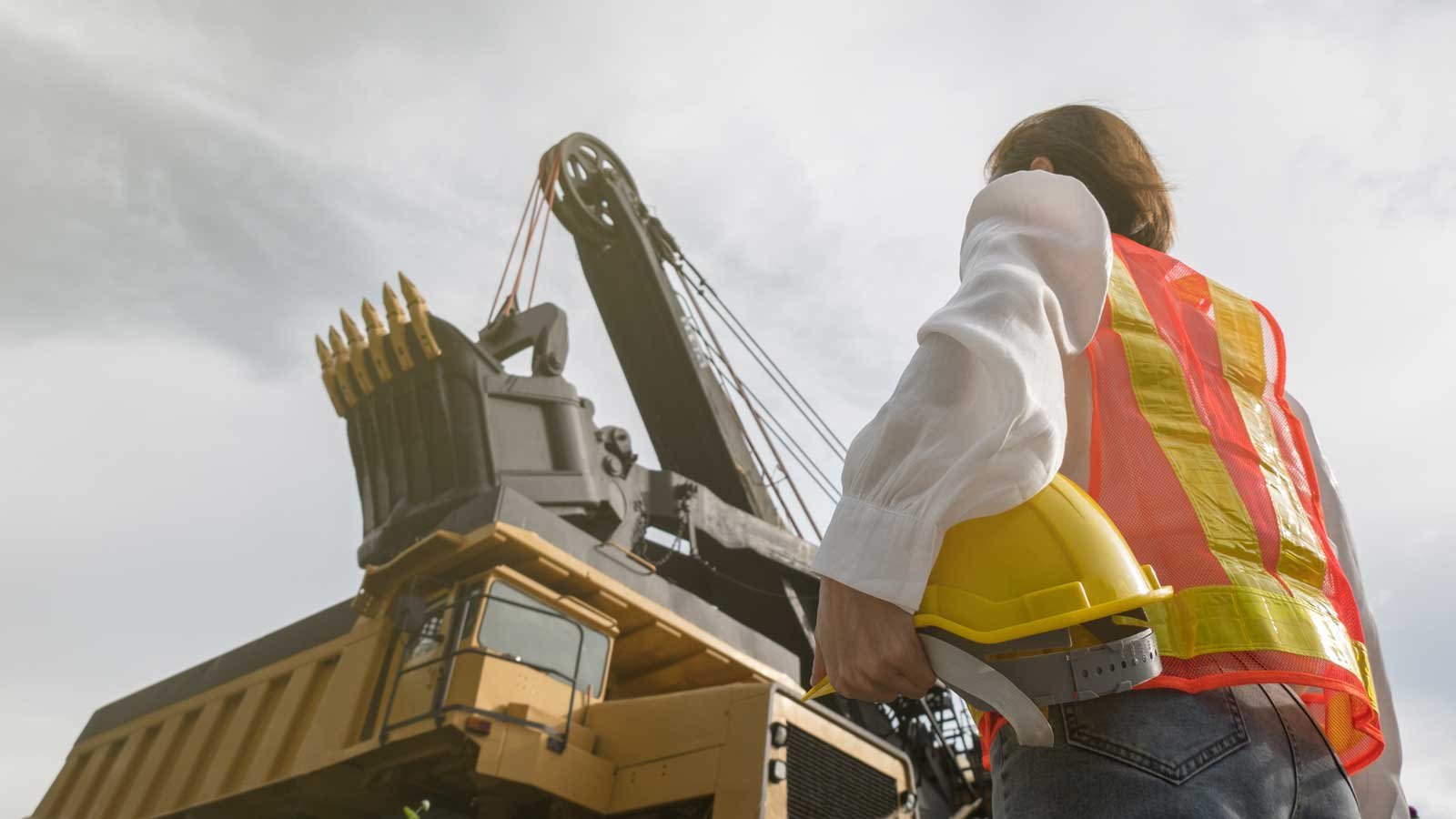
Avoiding Risk Assessment Pitfalls
Here we break down plant risk assessments and help you avoid common pitfalls.
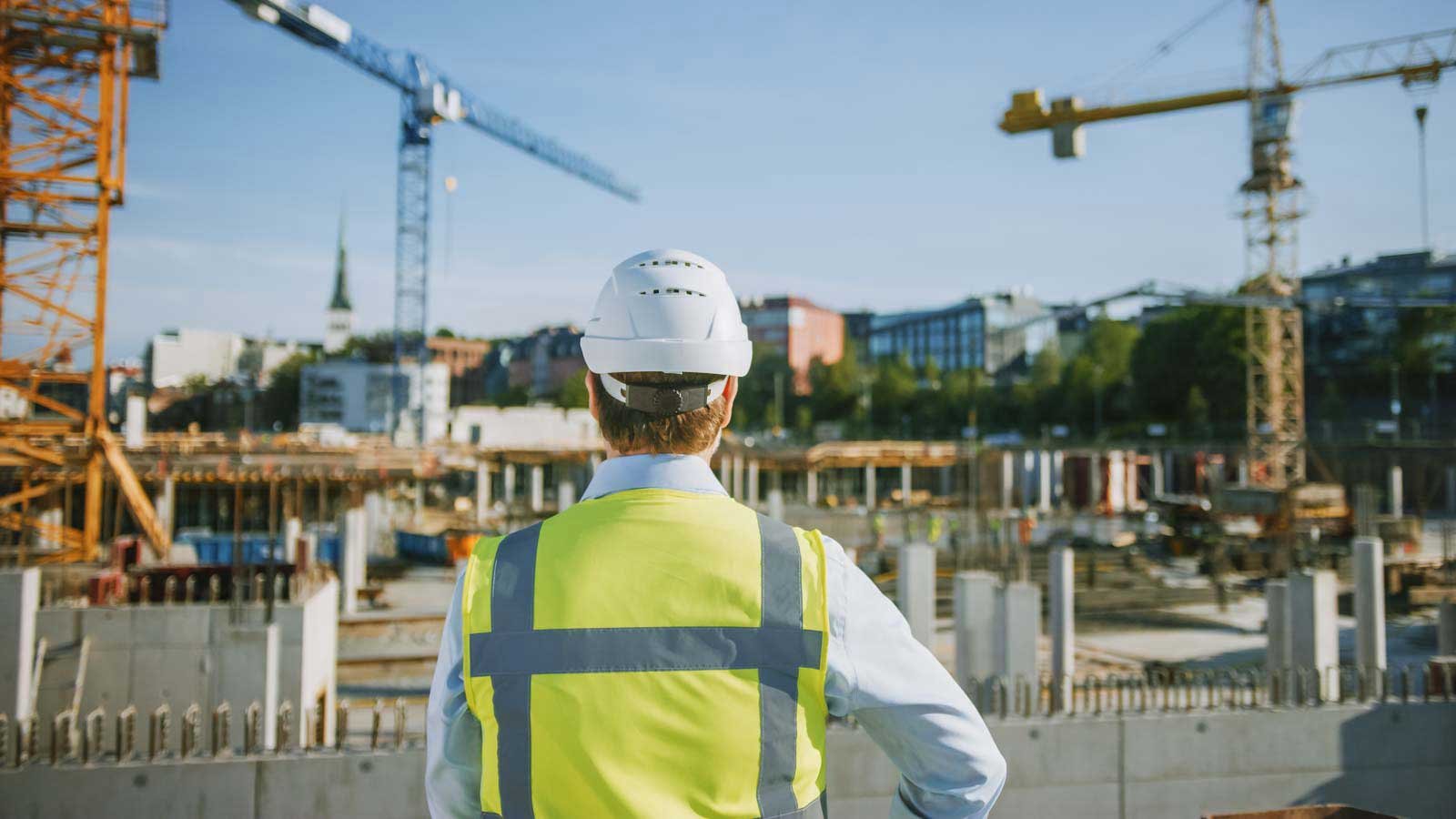
Benefits of Safety Management
Safety management is a consideration that should be made by all businesses.
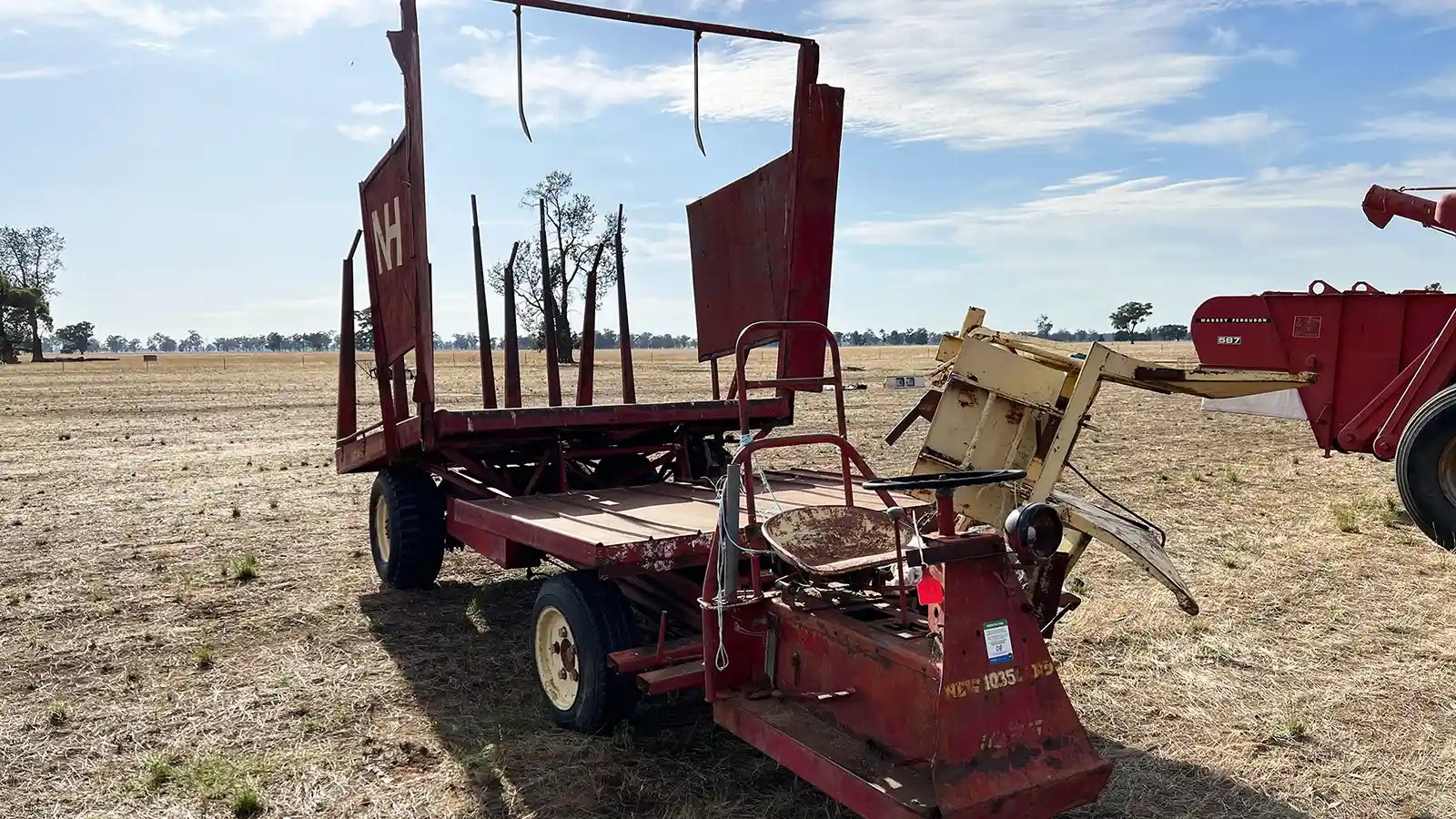
Clearing Sale Safety
Learn how to comply with clearing sale plant safety obligations in this guide.
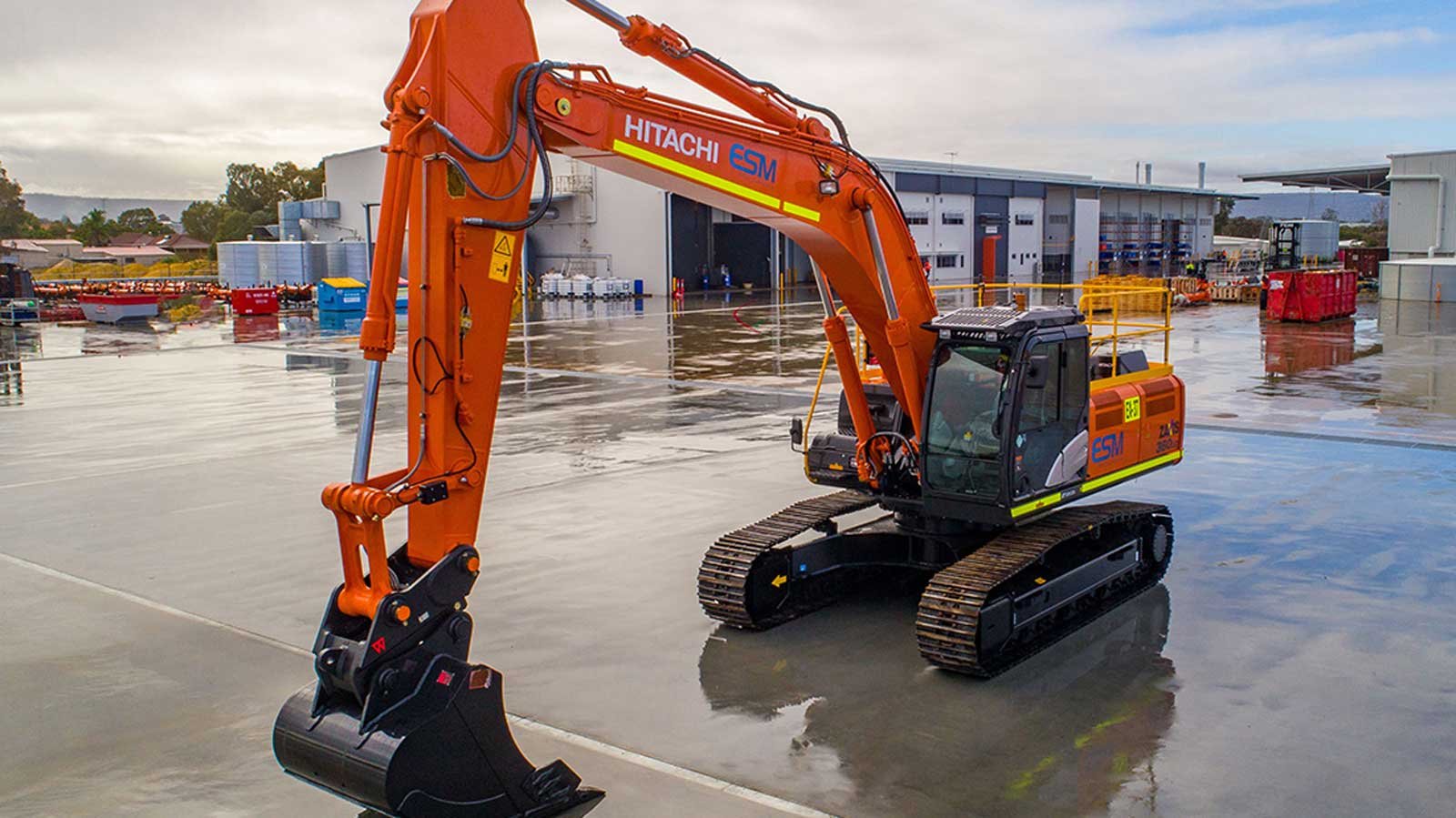
Excavator Risk Assessments
Find out how to conduct excavator risk assessments in this guide.
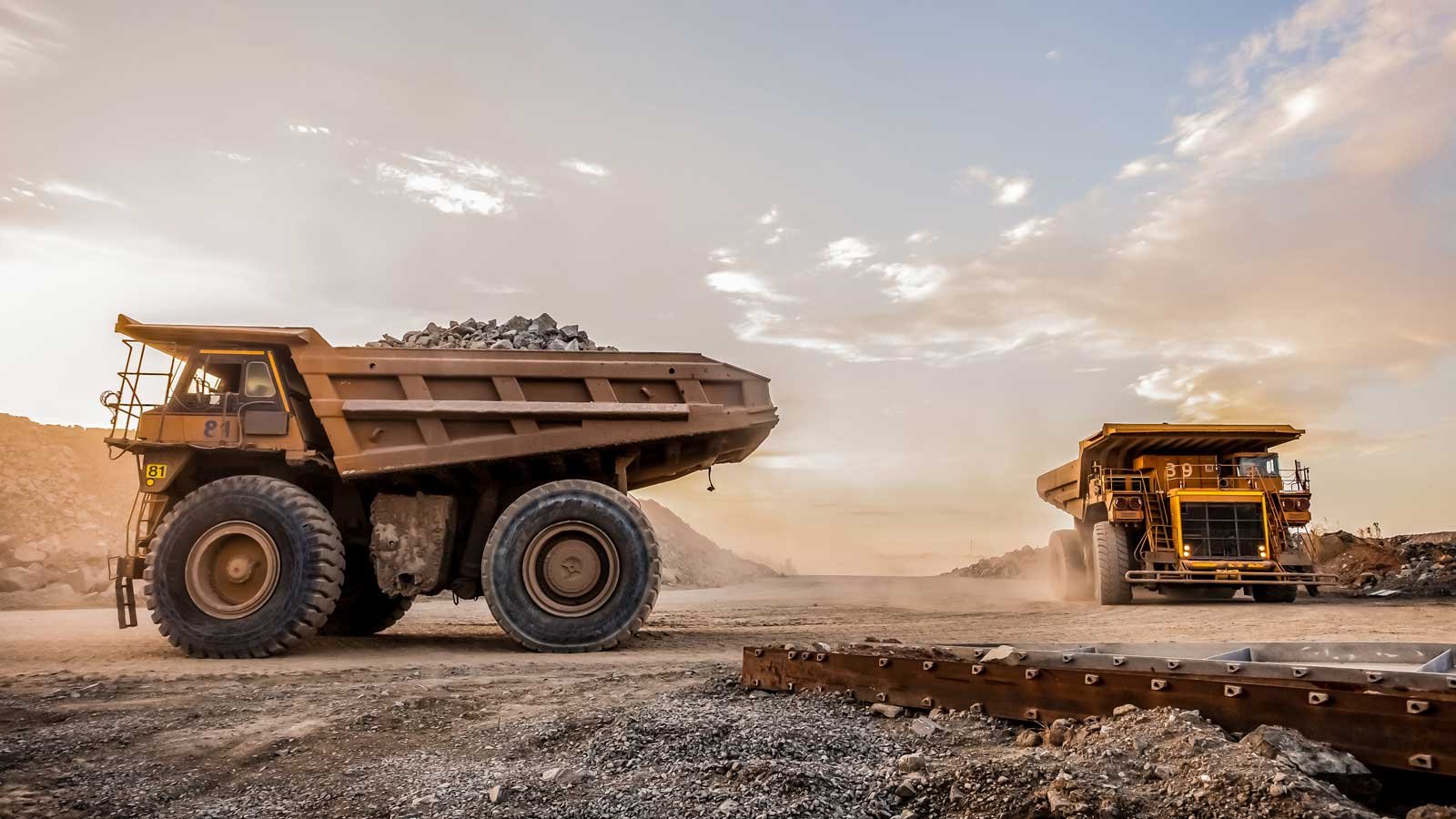
Mining
Plant Assessor has developed a special assessment purpose incorporating additional requirements of MDG15.
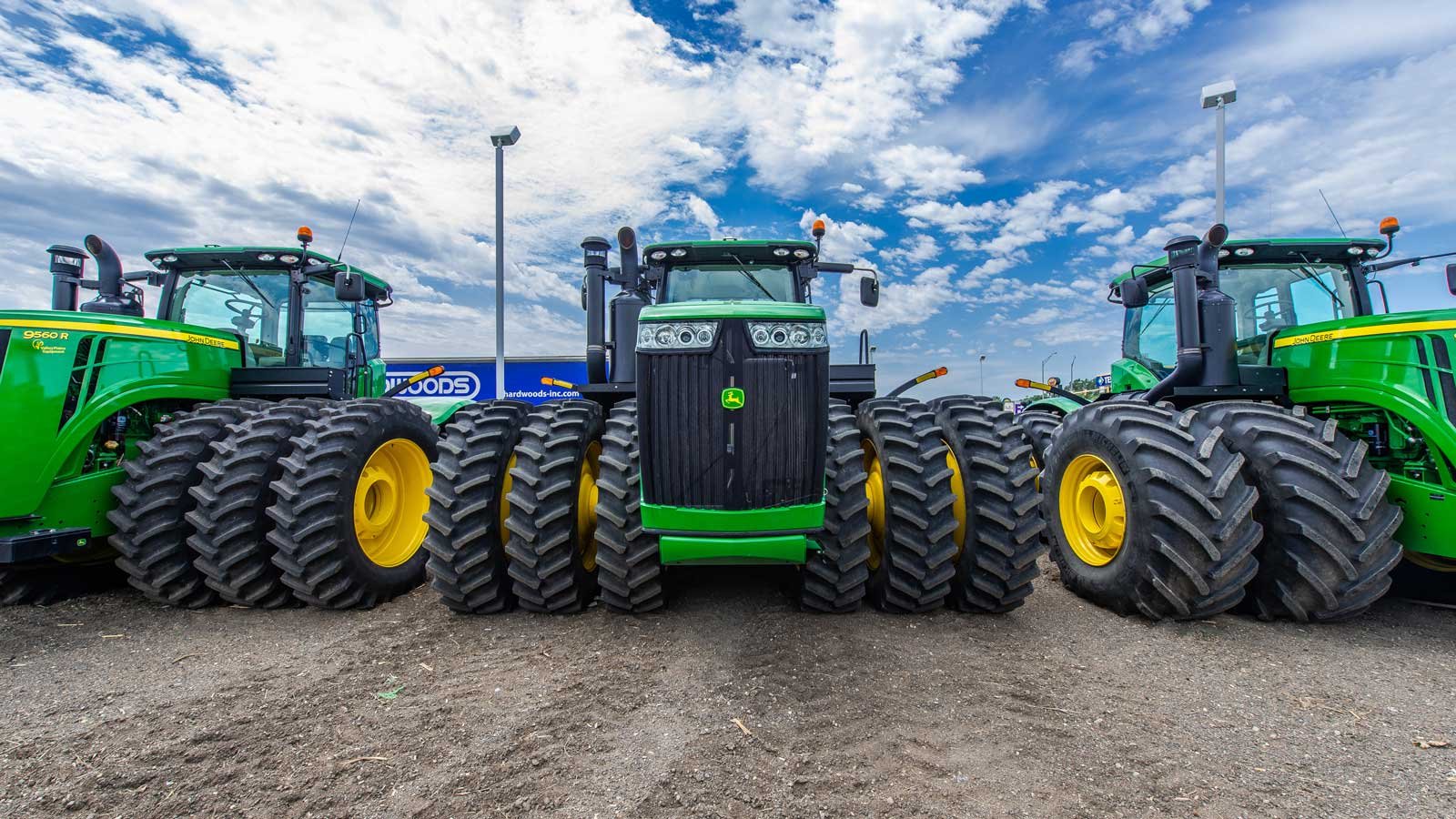
Obtaining Risk Assessments from Suppliers
Find out some tips and tricks about obtaining risk assessments from suppliers.
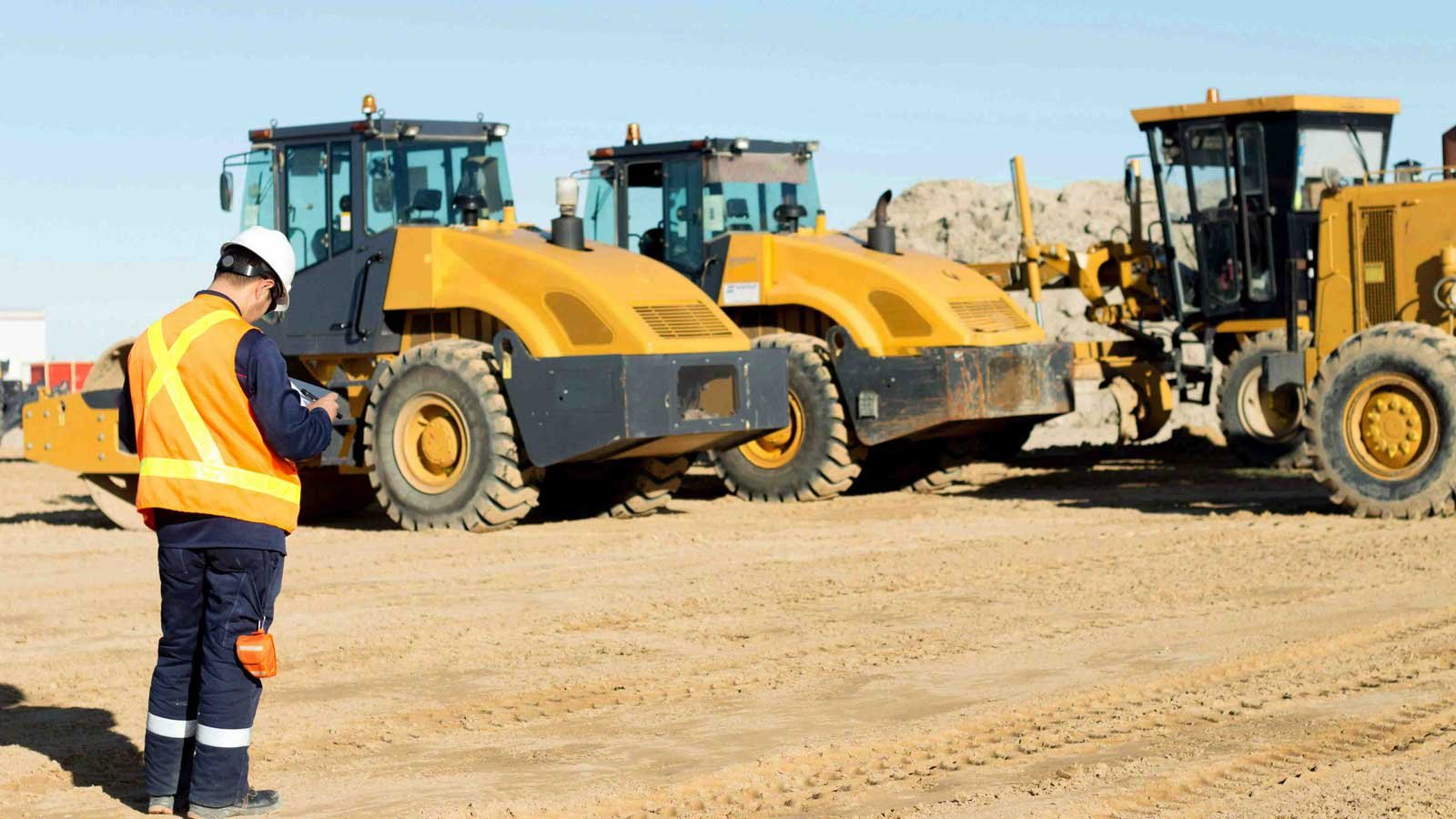
Procurement of Safe Plant
Safety is important to consider when purchasing a piece of plant.
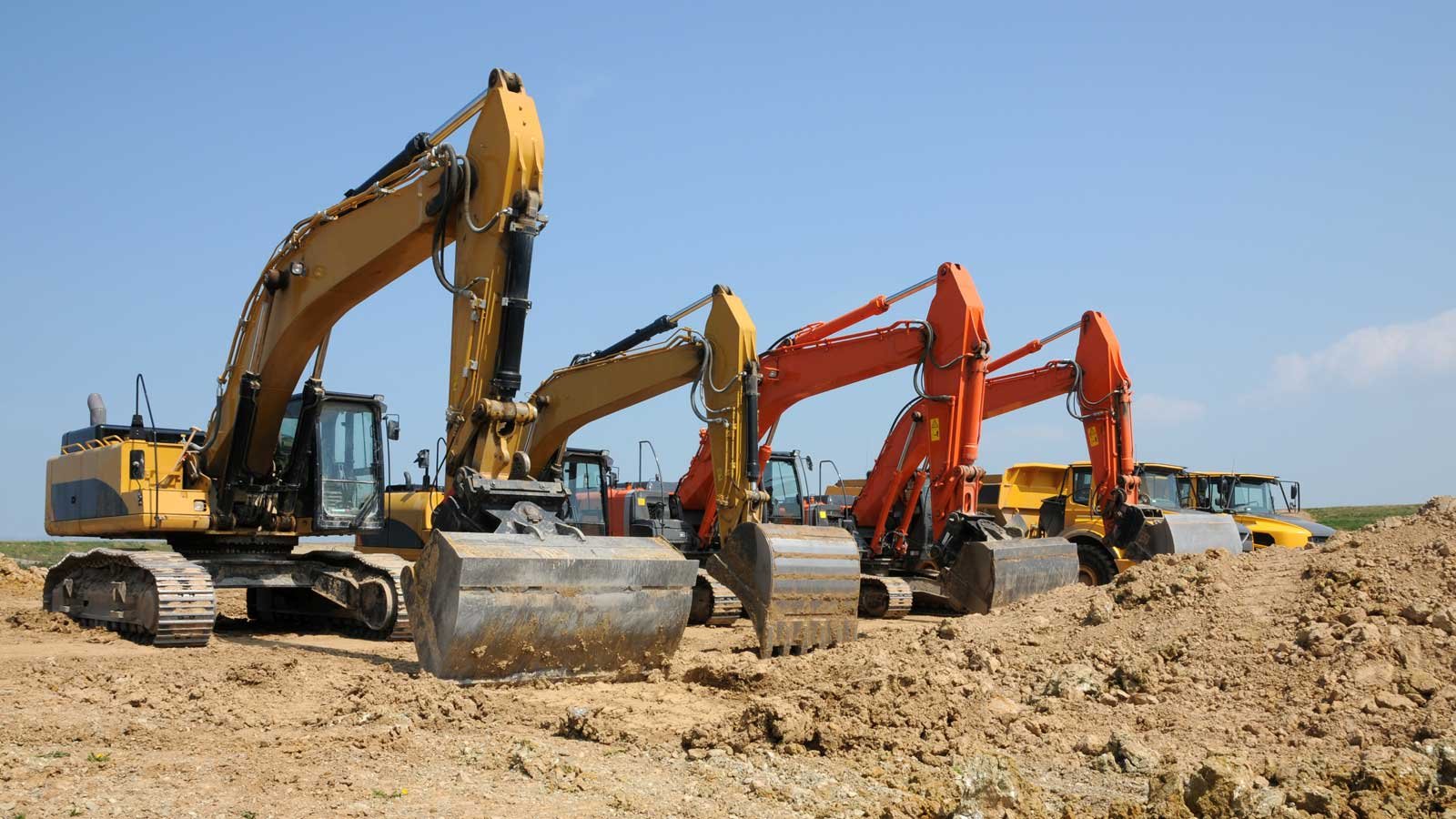
Risk Assessment Plan Overview
Plant Assessor can help users understand how to manage safety obligations.
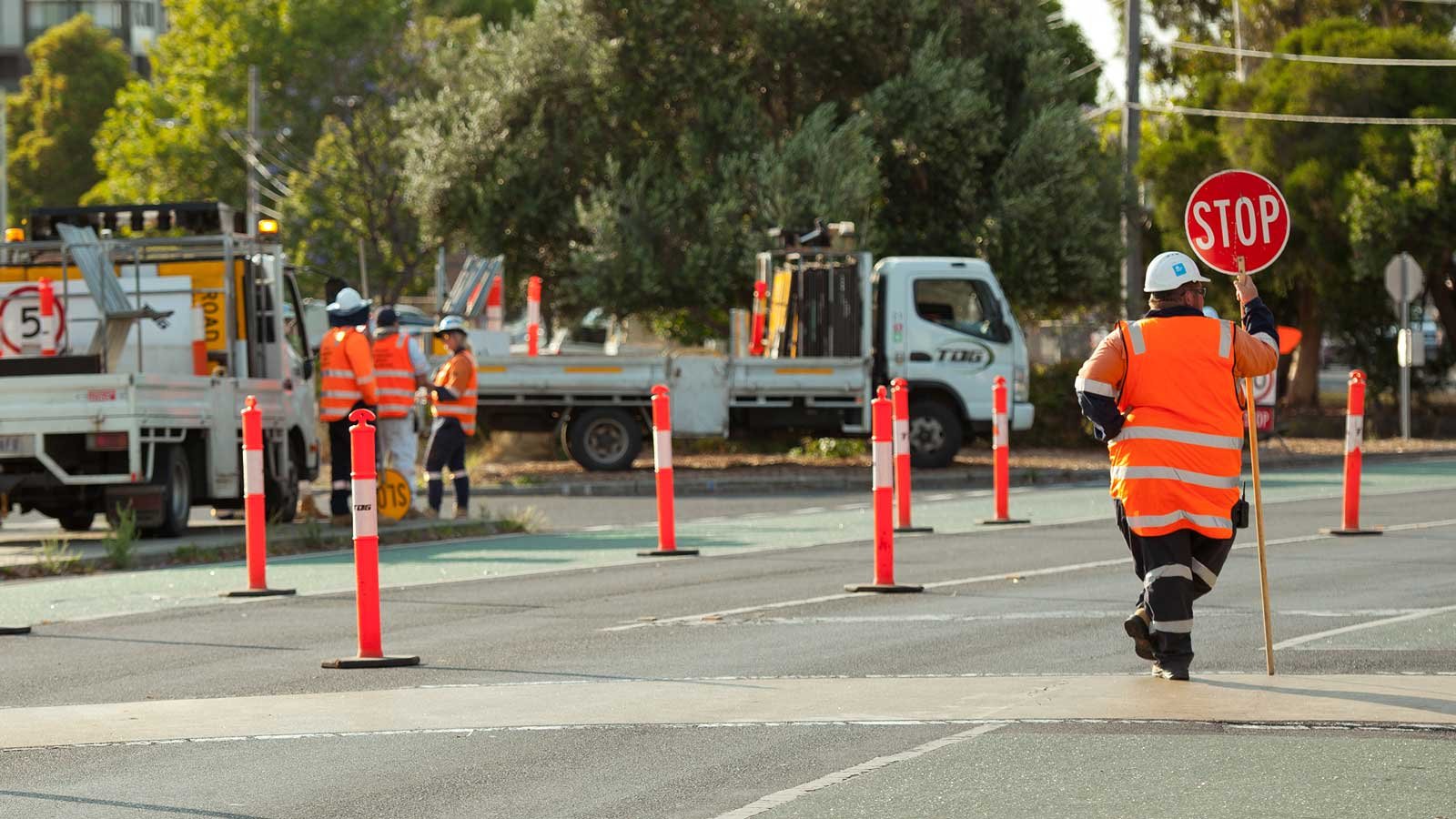
Procuring Safe Plant: Local Gov
How to procure safe plant and equipment - a guide for local government.
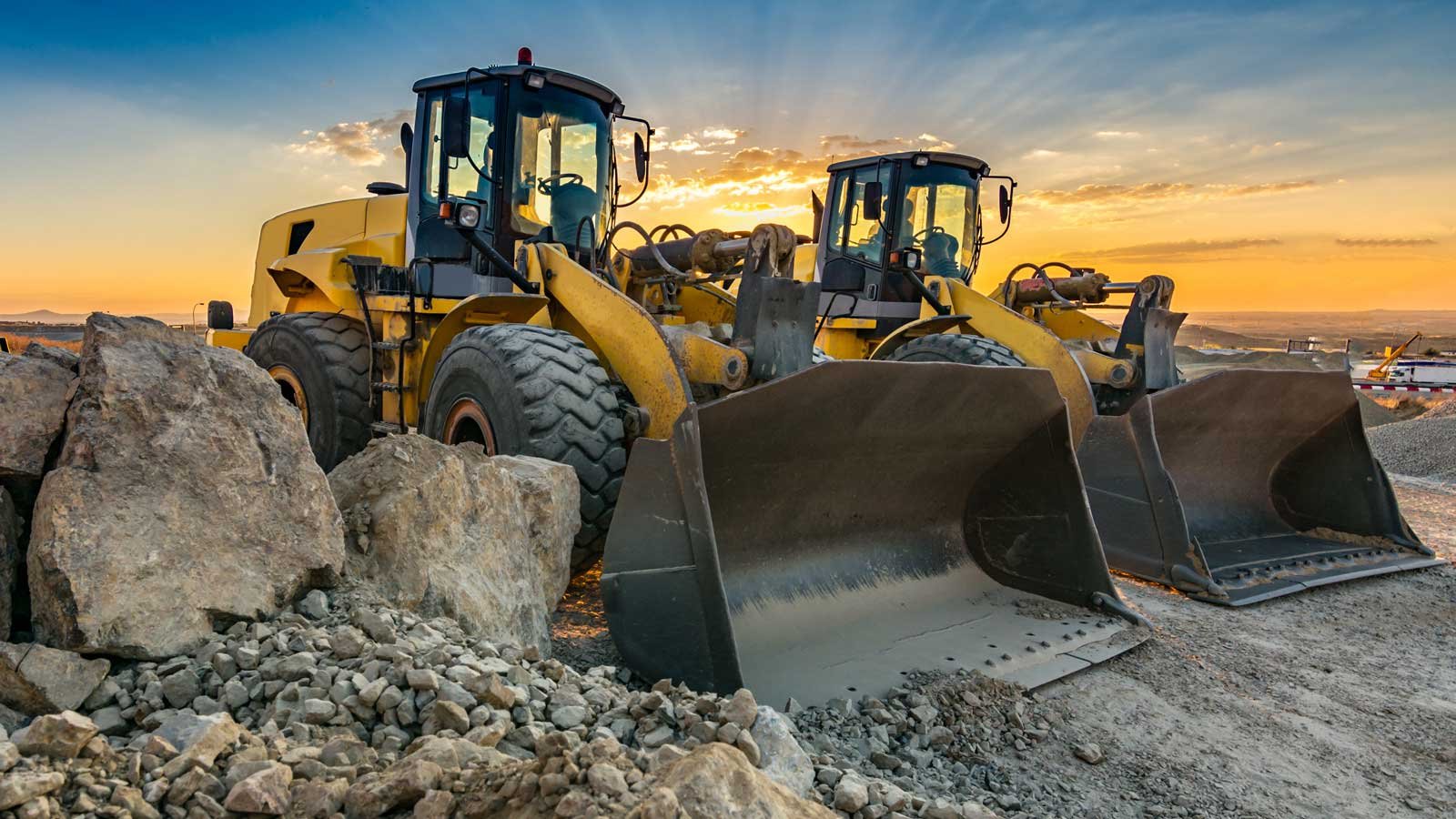
Simplify Risk Assessments
Our Machinery Compliance Engine takes all the complexity out of the risk assessment process.
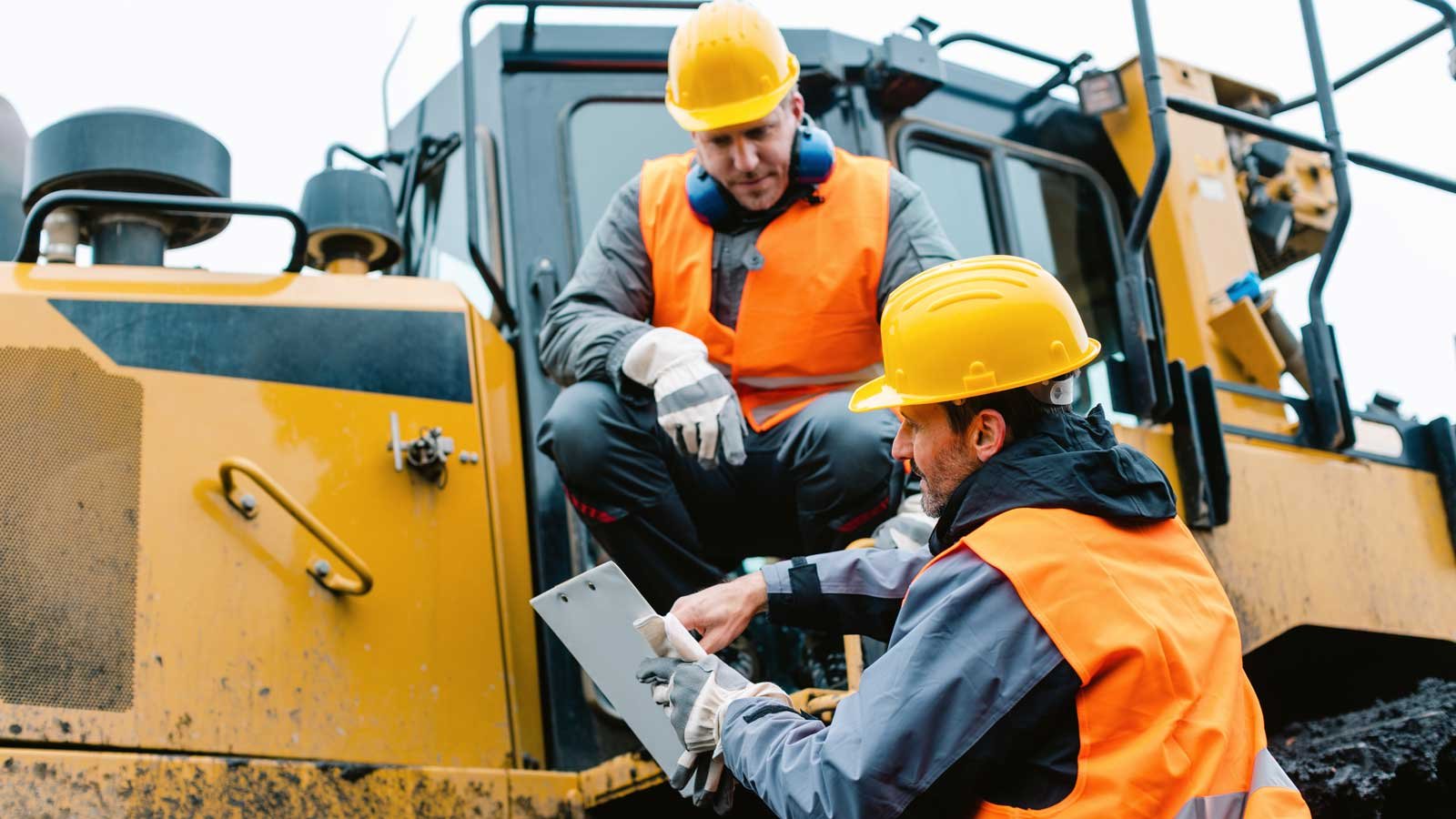
How to Ace FSC Audits
An on-site audit by the Office of the Federal Safety Commissioner can be daunting. Read more.
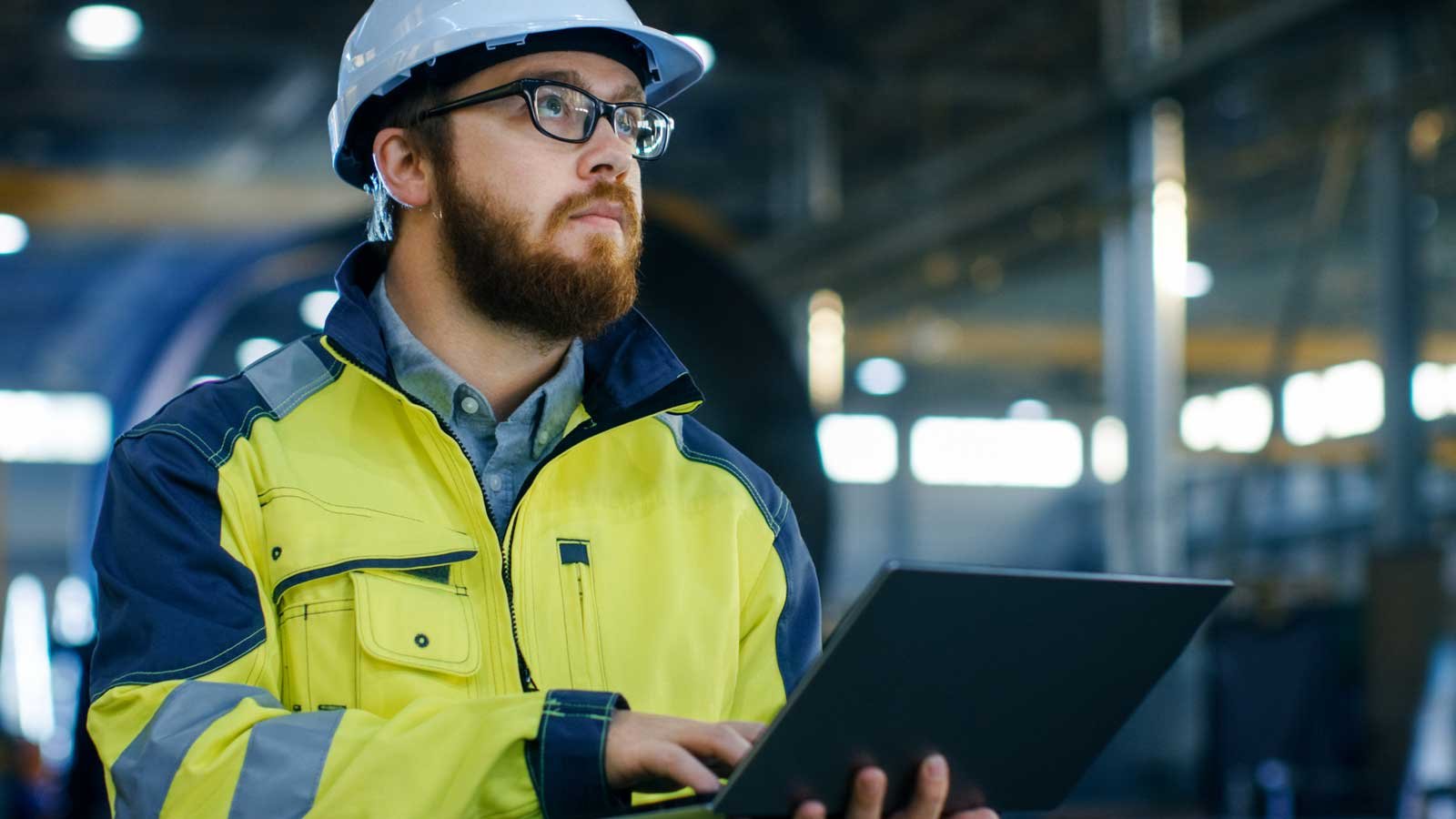
Entering Fleet into Plant Assessor
What's involved in setting up and managing a risk assessment plan.
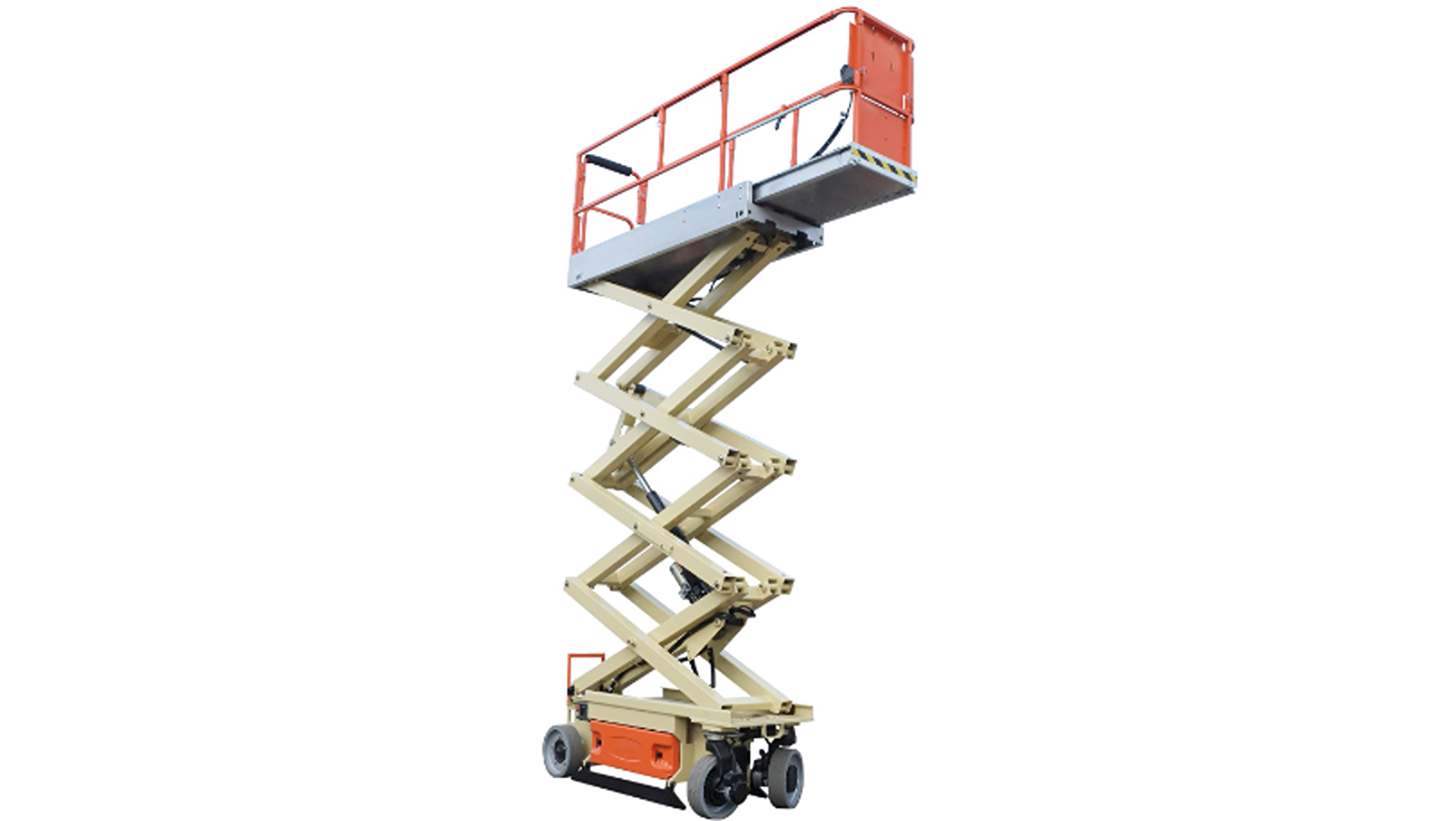
Elevated Work Platforms
There are two types of elevated work platforms - scissor lifts and boom lifts.
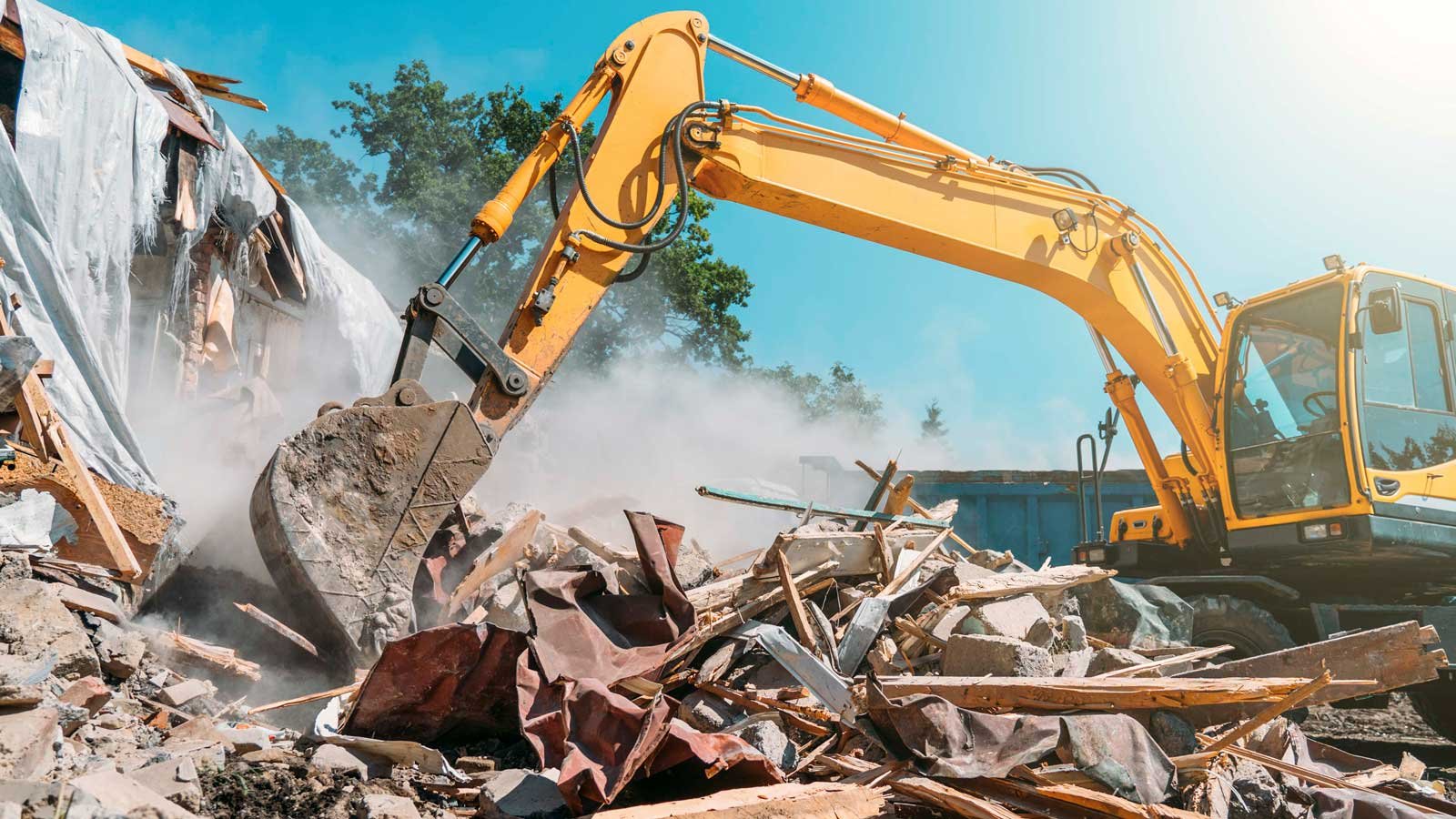
Eye vs Hook
Information relating to assessing a piece of earthmoving equipment.
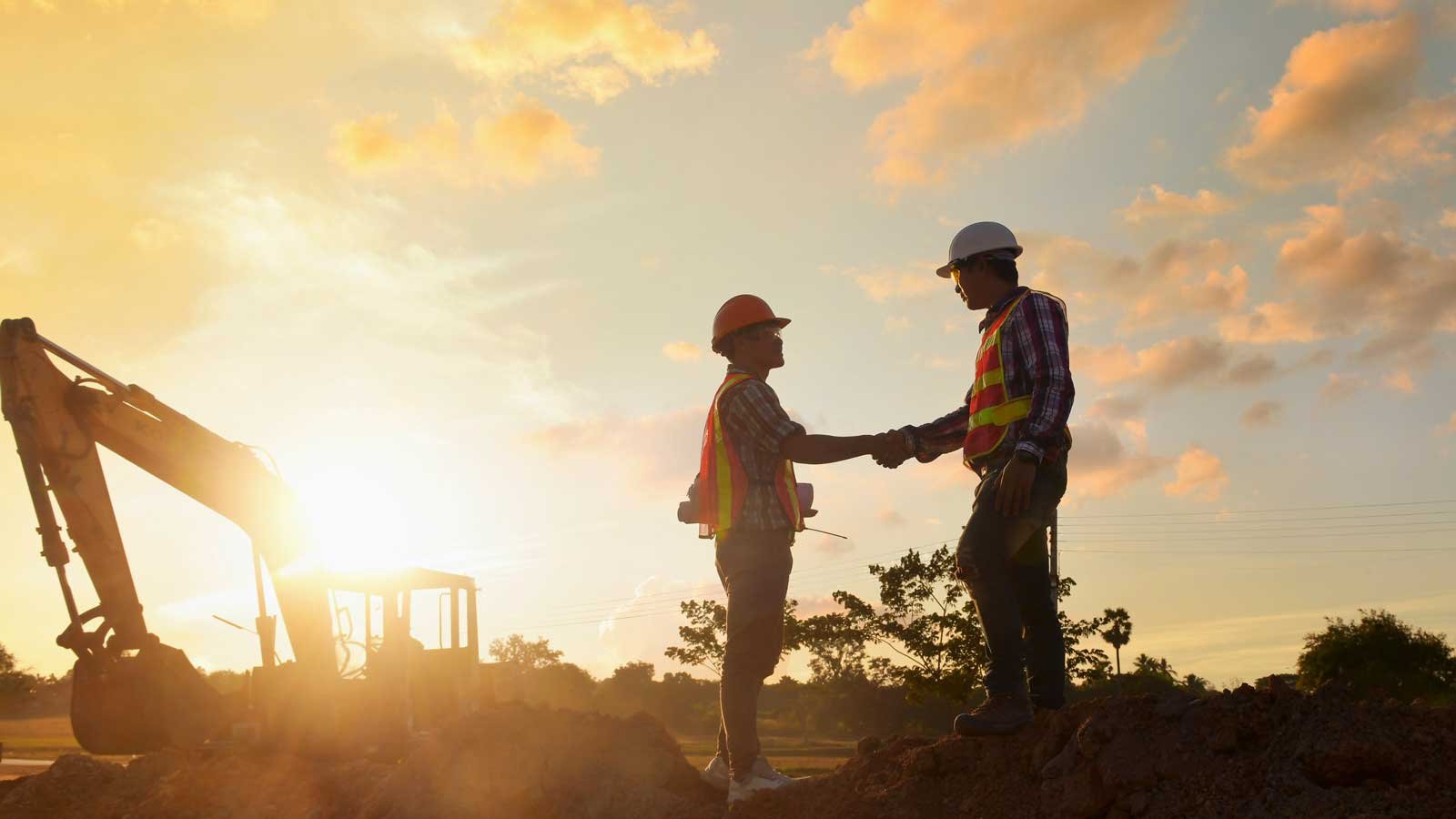
Simplifying Safety
The three key elements of a plant safety management system are safe plant, safe operator and safe environment.
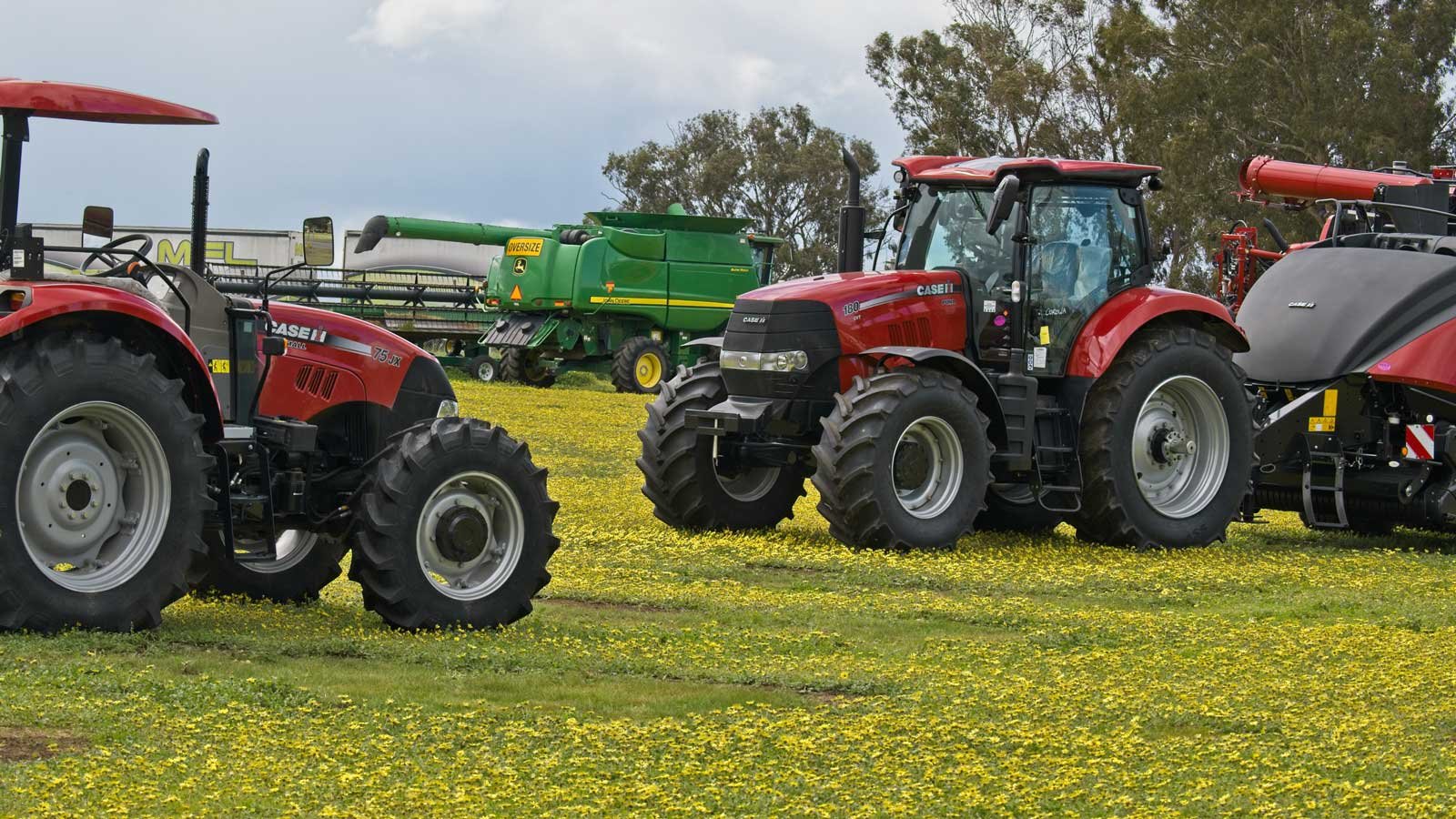
Tractor Risk Assessments
Plant Assessor provides a range of products and services to assist with your tractor risk assessment.
2 min read
What is a machinery risk assessment and why do I need one?
Apr 8, 2024
1 min read
Update to quad bike regulations in Queensland
Apr 8, 2024
Sign up for the latest industry news