Your machinery safety system is vital. It's the system that ensures you operate safe and compliant machinery.
Without an adequate machinery safety system in place, your staff, contractors and your business are at risk of catastrophic consequences.
Checking out the health of your machinery safety system on a regular basis is a great way to ensure your system is operating effectively. But do you have the time to develop a checklist for assessing your machinery safety system?
Diagnose your level of compliance
Know where to improve
What is the Machinery
Safety System Health Check?
At Ideagen Plant Assessor, we have developed a comprehensive Machinery Safety System Health Check to help you assess your machinery safety system. Simply answer the yes or no questions across the four sections to find out whether your machinery safety system is up to scratch.
Your safety system health check will assess:
Machinery pre start checks
Service scheduling and record keeping
Information management and sharing
Periodic machine inspection
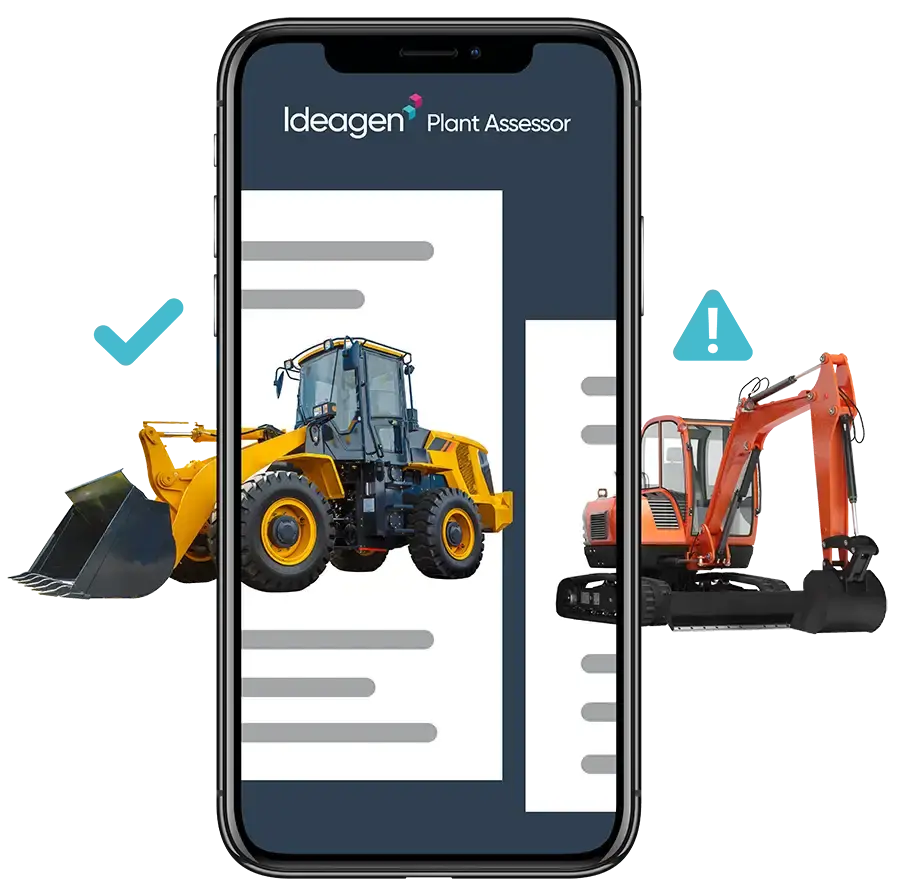
Once you have completed each section of the questionnaire, you will be provided with feedback on areas that may need improvement. You can also opt for Ideagen Plant Assessor's team of machinery compliance experts to send you a personalised report based on your results.
Does this sound like an easy way to check the health of your machinery safety system? Head to the Machinery Safety System Health Check now.